Who Buys the Hand Tools?
There are reasons to supply hand tools for your workers, and reasons to have them supply their own. October 3, 2006
Question
How many of you small shop owners require your employees to supply their own basic hand tools, for example tape measure, chisel, square, etc.?
Forum Responses
(Business and Management Forum)
From contributor A:
All of my guys except the clean up man work on contract labor. If you can pick it up and walk out the door with it, it does not belong to me.
From contributor B:
I'm the same way. Bring your own tools and leave with your own. Hand tools are the tools that break the most often and need to be replaced most often. A large sum of money goes into buying and maintaining them so if someone is always using them, dropping them, or stealing them, it adds up. I am going to have my guys design and build their own custom tool box that will have locks. This way they gain experience in design and building and protect their tools. If it disappears at the end of the day it is their fault - not mine.
From contributor C:
Any employee worth having will have his own hand tools anyway and should prefer to use them. There are too many different tools out there with too many preferences to provide for. As per the previous posts I have to agree whole-heartedly - let them be liable for their own equipment.
From contributor D:
I furnish everything and don't want personal tools in the shop or on the job site. I know the condition of my tools and what can be done with them and I don't want wasted time messing around with tools that don't meet my standards. I furnish tape measurers, pencils and safety glasses as well.
From contributor E:
I buy and own all the hand tools for my shop. I buy very high quality tools and I buy what I like to use. I also let my guys use my tools to do side jobs or home improvement projects as long as they clear it through me. In fact I even set stuff up for them as it comes up. Here is an example - a guy came to me who goes to my church and asked if I could help his son finish his cabinets (the guy is 65 or so; his son is about 40). Seems he thought that you could just buy a tablesaw and a kreg jig and it would take no time at all to build cabinets. He was up against a bank deadline and didn't have any doors. He had purchased router bits from Harbor Freight and was going to make 85 hickory doors. I took 10 minutes and taught him how to figure out his door list and ordered his doors from a local door company. I marked them up 25% and finished them with clear lacquer for $15 a door. I charged $5 a door to hinge them and $3 for the hinges and plates. At this point he wanted us to come out to his house and mount all the doors and drawer fronts and crown and hardware and toeskin. I didn't want to touch that with a 10' pole so I told him that my guys would be glad to help him after hours and that they could work out an hourly wage. My guys made $25 an hour and I didn't have to touch the mess.
I let my guys use my hand tools, drills, bits, impact drivers, table saw, chop saw, compressor, nail guns etc. They were happy to deal with the mess and make the money. Now, if they were to leave my shop and go to another shop they would have to buy all their own hand tools at once. If they own their own hand tools then what is to stop them from going and finding their side jobs until they have more side work than full time work? It is very hard to find guys who can learn and guys who will show up. If I do find these people, I try to keep them. Not having their own tools is one way to keep them and they think it is because I am nice and don't want them to have to spend their money on things like tape measures. This works for me.
From contributor F:
The last shop I worked for required all woodworkers to have their own hand tools and cordless drills. Employees were given a list at hiring, and had to have all the tools within a short window of time. You were also given a bench and spot for your toolbox. Most of the guys who had some experience had built their own boxes and had many more personal tools than were required.
To contributor E: I think maybe you are a nice guy. After all, another way to look at it is that it's more of a hassle to leave a shop if you have to move a huge tool chest, than if you can just walk away. I guess it depends on the size of the shop also. The shop I used to work for had about 30 guys on the floor. That's a lot of hand tools to buy and keep track of.
From contributor G:
This is an illustration from a compilation of articles called "Extracts from Chordal's Letters". These were essays about life as a manufacturer in the 1880's. This book has one chapter called "Outwitting the Almanac". It discussed how to balance your workload over the course of a year in order to take advantage of the long days of summer daylight while mitigating the short daylight hours of winter. While today we talk about things like CNC and software, back then they were talking about how to light the factory.
The amazing thing about this book is how much things are still the same 125 years later. In one article the author, James W. See, speaks of the various ways individual workers manage their personal space. The picture pretty much sums up one of the possibilities he speaks of.
About two years ago Boeing Airplane Company finally rolled the last personal toolbox off the shop floor. As it turned out these toolboxes were personal fiefdoms to be managed as the owner saw fit. In some cases the carts just held potato chips and extra clothing. In all cases the workers were paid at the beginning and end of each shift to roll the cart from where it was stored to where they were working. In some cases this was a considerable distance. A problem that developed during the workday was that these carts held more tools than were necessary for the task at hand. At the same time they wouldn't necessarily hold the tools that were needed. Often the tool boxes were something you had to walk around or were inevitably on the other side of the airplane from where you were. Boeing's response to this was to provide tool kits, holding what was necessary, where it was needed. In some cases these tools were color coded for the task at hand.
If you provide the tools you have more input about what kind of tools they are, what kind of condition they are in and where they live in the building. These kinds of controls are significant if you are trying to introduce any simplification or standardization to your processes.
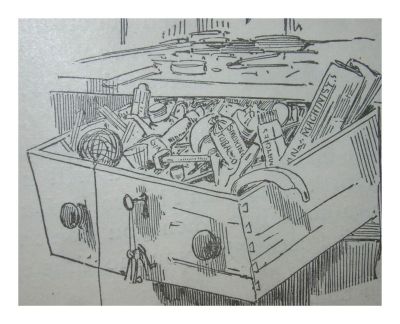
Click here for full size image
From contributor H:
We provide all tools, and yes - we lose quite a few each year. Each bench has a place for each tool and there is an open shelf nearby for the rarely used tools that don't warrant one at each bench.