Vacuum Pump Performance, Pump Size, and Altitude
Here's some in-depth and thoughtful discussion of vacuum pump capacity and the factors that influence pump effectiveness. January 7, 2010
Question
I'm researching a potential purchase of a CNC for a small furniture and cabinet shop near Telluride, CO. This would be the first CNC I've used or owned. The shop is at around 7500 to 8000 feet altitude. One CNC salesman that I spoke to said that I would need a vacuum of about 40 hp for this altitude and that they cost around $20,000. Does anyone have experience using the vacuum at altitude? What other options are there for holding down sheet goods and cutting out cabinet parts? I vacuum press veneer in a bag which works fine, but I imagine keeping wood down for routing is a different animal.
Forum Responses
(CNC Forum)
From contributor B:
This CNC salesman is giving you a bum steer. Either he is trying to sell you a larger vacuum pump or has no idea what he is talking about.
Two things:
1) A larger size vacuum is needed when holding your part requires a lot of air flow. A larger vacuum pump will not create a larger vacuum; it will just pull more air.
2) If you are at an altitude of 7000 to 8000 feet, the atmospheric pressure will be around 70% to 75% of the pressure at sea level. In many cases that is not enough pressure drop to affect the hold. A part with a footprint of a square foot will have over 1400 lbs force holding it at 10 lbs per square inch vacuum (which is about 70% of 14 pounds).
Now I am not going to argue that there might not be some situations where there will not be as much hold at a high elevation as there is at sea level. I don't know what you do or what type of parts you make, but most likely it will not affect your ability to hold them to the table with a vacuum.
The larger vacuum will do one thing and one thing only, and that is pump more air.
From contributor T:
I don't like the use of the word "vacuum" in this context. Strictly speaking, vacuum is a volume which has no air in it at all. This is not the case with CNC machines, as the pump doesn't remove all the air. I have been told that the negative pressure that pumps usually produce is about -0.7 bar. This is relative to the surrounding air, so no matter how high you are, the pump should always operate at the same negative pressure, in my opinion.
In these vacuum systems there are always leaks through valves and seals, so the more there are of these, the bigger the required pump will be.
If altitude does cause problems with vacuums (I don't know whether it does or doesn't), then maybe you should stick to a machine with a single vacuum system instead of a double vacuum system.
From contributor D:
The best way is to check it for yourself. I told the Stiles machinery guys that the Schmaltz components in their machines didn't work very well for small solid wood parts in our doors. They took this as a challenge and flew me up to Grand Rapids. I had a few pieces of Sapele about 18" long by 5" wide. I explained that I was cutting tenons with a large cutter and the force would be from the side. Well, every time they turned the suction on, I could slide the part off with very little force. The salesman kept saying to the tech to show me the machine would cut a tenon for me, but the tech was nervous now, and didn't want to throw the part, and refused to run it. They bought me lunch and flew me back to Charlotte...
From the original questioner:
Contributor B, thanks for this information. It's a helpful reminder of something learned long ago that does help put some perspective on the salesman's claims.
From contributor I:
Absolutely, increasing altitude decreases atmospheric pressure available for hold-down force. A rule of thumb is that a pump’s maximum vacuum (typically measured in inches of mercury in the US) will decrease about 1” per 1000’ of elevation. So a pump that can achieve 26” Hg at sea level could only get to 18” Hg at 8000’, a loss of about 30%.
While a 30% reduction is significant, you still have plenty of potential hold-down force to work with; you just have to be more efficient in preserving it. A real-world example, in our Greensboro showroom (so there’s no reason you can’t get satisfactory vacuum performance at 8000’ and you don’t necessarily need a 40 hp pump to get it). You will have to raise the threshold for the size part you must onion-skin (~200 in˛). More power would let you be less conscientious with how you conserve vacuum, but you have to decide if the increased power bills and pump cost is justifiable.
P.S. Cutting pressures on solid wood, i.e. door components, can easily exceed vacuum hold-down force regardless of pump size or altitude. Clamp these parts if at all possible!
From contributor T:
I have also heard stories about Schmaltz arms that use a double vacuum. The problem is, they use a vacuum (1 bar max) to hold the cups or clamps to the arms which apparently isn't strong enough and thus may slide. I know the SCM Prisma uses a pressure (not vacuum) of about 8 bar to hold the cup/clamps to the arms, which is very difficult to budge.
From contributor E:
Please read the recent posting of the Shop Sabre user that can not hold parts down with a 25 HP regen blower. Also note that the same people that advise you are mislead by the suggestion of using the 40 HP pump offer no specific recommendation of their own. Notice how regenerative blowers are offered on routers under $50,000.00? Do you really think it's because they are superior to high pressure vacuum pumps? Then ask yourself why so many people post here complaining of part movement with the OEM supplied 10 HP Becker for example. You get what you pay for and there are no shortcuts, guys. You think the guy with the KOMO really wants to spend more money on a 25 HP or larger high pressure vacuum pump if they could use a blower? C'mon.
From contributor J:
I will agree with contributor E on this one. Earlier today I ran some MDF doors and drawer parts with 1/2 inch Baltic. I ran it at 200 ipm using a 10hp blower (FPZ) without any problems at all. I think the real deal is I accept the limitations of level of machine, level of investment, and reasonable expectations of time to produce. Big iron has its place but would be massive overkill in the work that I do as I have no interest in high production - none, zip, nada. I can cut cabinet parts at 300+ ipm and drawers at 200. It is the difference of 10 minutes one way or the other and personally I am okay with that. I am with contributor E on the 250 Busch or Becker and even many of the larger CNCs I watch for sale use these two at a time. It is unrealistic to think a mid weight machine will run as fast as a 15000# Komo, but then again for the price of one of them I can afford 2-3 with Beckers and run circles around them in speed if that was my goal.
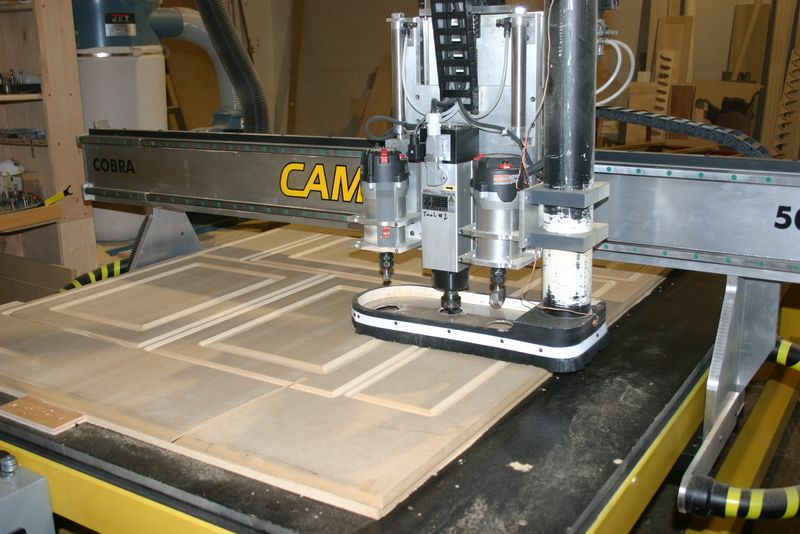
Click here for higher quality, full size image
From contributor R:
With vacuum hold down it is all about differential pressure. I use gasketed forms for specific solid wood parts with a 1.5 hp rotary vane pump. It works great and I can get up to 22" hg vac, put a piece of MDF on and it won't work at all because the free air CFM is 25 CFM and MDF is slightly less pervious than an air filter. So for that I use the most powerful vacuum cleaner motor that Granger sells. Like a regenerative blower, it moves a whole lot more air at lower static pressures. Need more air, add more vacuum cleaner motors. I would run them in parallel (plumbing wise) if the cutting you need to do is exceeding the atmospheric pressure you can garner; other hold down strategies can be employed but the ambient pressure is the limit, no matter how much hp you apply.
From contributor E:
Wow! I sure could have saved a lot of money over the years if I knew I could replace the Sullair vacuum pump with my wife's Hoover. Proves you learn something new everyday.
From contributor D:
Have to say I'm surprised to hear vac motors from Grainger work for you, contributor R. A few years ago our 10hp Becker went down and I couldn't wait a few days for the replacement and rented the biggest commercial shop vac in town. I hooked it up to our pod and rail Masterwood and got almost worthless suction. I tried tying in the old dust collector for the machine, a 15hp three bag unit, with not much better results. I have few problems with a system on our SCM Prisma, which employs supercharged compressed air to mechanically clamp the pods down and a 12hp Becker for part hold down. It has an automatic cutoff if the pressure drops below .8 kPa to help prevent throwing a part. I still wouldn't mind hotrodding our Masterwood with better hold down, but I'm a bit skeptical after past experiences. Maybe I was doing something wrong.
From contributor R:
I only have small machines, the blank size I am cutting is 30X49, and I use a specific sealed and gasketed form as it is always the same layout. The point is that if you can develop sufficient differential pressure you can hold the parts. Under the right conditions, a smaller pump may perform as well as a very large one as neither can create more than 1 atmosphere of vacuum.
From contributor U:
There are shops in Louisiana that have problems holding down small parts. They do not have an altitude issue. There are shops across America that employ Pods. But not all of the Pods hold down all of the small and narrow custom parts their shop is trying to produce.
I agree that the best and surest and eventually quickest solution could be to create a custom fixture for those small and narrow custom parts.
I know contributor R is on the right track with his statement about "a specific sealed and gasketed form." Give a closer look at vacuum surface area or the dimensions and density of the inexpensive sealant on the fixture before purchasing the expensive larger vacuum system.