Troubleshooting Planer Chatter Marks
A pressure bar set too high may be the source of chatter marks on planed boards. May 28, 2006
Question
I'm getting cross grain marks evenly spaced on everything I run through my 20" Grizzly 1033 planer. Just replaced the bearings and cutterhead and again set up the chip breaker, pressure bar, infeed and out feed rollers, and bed rollers after a fresh set of knives set with magnetic jigs. Any suggestions other than making a boat anchor with it? A new one just isn't in the budget right now.
Forum Responses
(Solid Wood Machining Forum)
From contributor D:
I have the Craftsman Professional 20" planer, which is very similar to yours. I was getting those same marks on mine and found that the pressure rollers were exerting too much pressure on the wood, causing the marks. I backed it off a little and have had no problem since. If it's not your pressure rollers, it could be that one of the knives you installed might not have been ground right. Was it leaving the marks before you changed the blades or after?
From the original questioner:
I've tried 3 new sets of knives (within the last year) with the same results and set the rollers to manufacturer's specs. I've owned this planer for 10-12 years, and this one's got me stumped.
From contributor D:
I’m sorry, on my first post I meant to say the infeed rollers were my problem, not the pressure rollers (need my second cup of java). Now the pressure bar is something that may be causing your problem. The pressure bar is located behind the cutterhead and keeps the newly cut surface from bouncing up into the cutterhead as the stock enters and exits the planer’s feeding system. During the cut, it performs a hold-down function when feeding warped stock. If it is set too high, the wood will flutter and a washboard texture will result. And it’s likely that end snipe (a slightly thinner section) will occur. If it is set too low, feeding will be impeded. A majority of surfacing problems can be traced to this component, so its position is critical. I normally set a pressure bar about .002 to .004 in. above the cuffing arc for surfacing face-jointed lumber. For surfacing lumber that is rough on two sides, a slightly higher setting usually works well. Another consideration could be the bed rollers. The bed rollers reduce friction as stock is being fed, and they prevent premature wearing of the bed tables. So, it’s important that the rollers turn easily and are aligned precisely. If they are set too high, the wood could vibrate up and down, causing a washboard effect as well. Just some food for thought.
From the original questioner:
Not the greatest picture, but I hope it helps.
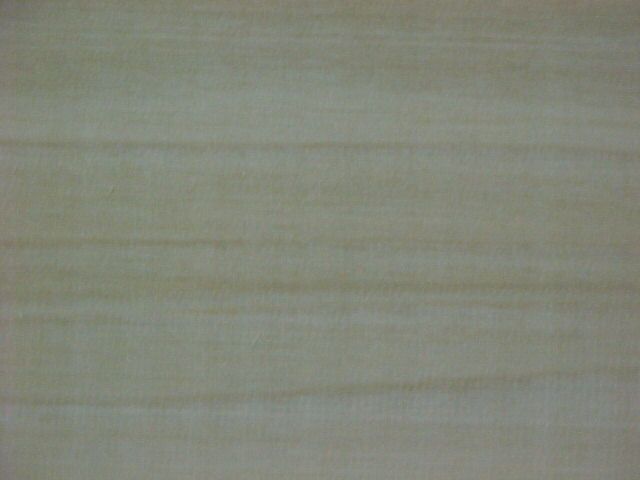
Click here for full size image
From contributor P:
From what I can see, I would say your pressure bar is not exerting enough pressure, thus too high. Also, how solid are your table jack screws? Put a dial indicator on your table while feeding, to see how it behaves.
From contributor L:
Do you lock the table for the last pass? I would lower the bed rollers completely, wax the bed real good, lock the bed table nice and tight and run a board to see if the problem is still there. If I need to run wet, rough wood, I might use the bed rollers, otherwise they stay down.
From contributor D:
I have to agree with contributor P. Drop the pressure bar a tad and see what happens.
From contributor W:
The best way I have found to set the pressure bar is to take a piece of timber at least 4 inches high by 3 inches wide and pass it through with the jointed surface down. Cut off a section short enough to pass under the pressure bar without contacting any other feed components, about 4 inches. Disconnect the planer from its power supply, rotate the cutterhead so the knives do not face the table, and pass the piece through by hand. It may take a bit of doing to pass the chipbreaker. Using the cutoff as a gauge, the pressure bar should be in good contact across its whole width. Too much pressure and it will restrict feed. If it is spring-loaded as mine is, you can run it at about the same height as the cutting circle and rely on the springs to give as needed. Other factors are degree of spring tension, flatness of table, and straightness of pressure bar. If warped or worn, it's not a big deal to have it ground straight. This is an area where there is considerable difference in machine design and construction, probably because the pressure bar is tucked away out of sight. An Oliver or other good old American planer will usually have a massive pressure bar, weighing about as much as a modern Delta planer.
From Gene Wengert, Sawing and Drying Forum technical advisor:
In most planers, the chip breaker is spring loaded, but the pressure bar is fixed (but adjustable). After a knife cuts the wood, the cells of the wood spring back slightly. If the PB is set in perfect alignment with the knife's deepest cut, the wood will be too thick and will not feed well. So, the PB is usually set a few 1/1000ths of an inch more open. Where we sometimes see problems is that the bed plate will wear in the center (and not the edges so much), as that is where all the wood is rubbing as it passes through. A narrow piece of wood sent through the center of the planer will not be held tightly against the bed plate and will chatter. A wide piece will not, as it is held at the edges. So, try two different width pieces and see if you get the same marks.
Are you old enough to know what carbon paper is? If so, find a sheet of it and rub it gently on the wood surface after planing. This will highlight the marks. Now, are the marks spaced identically and possible in a repeating pattern or are they random? Chatter is random, but problems with setting the knives or other rotating object will have a repeating pattern.
From Gene Wengert, Sawing and Drying Forum technical advisor:
One other important concept in planing is that the end of the lumber must always be supported both as it enters the machine and when it leaves the machine. If the top head is first, then the lumber must enter the machine with the end just a fraction high. This will avoid snipe in the front. Then on the exit, if the top head is the last head, the leading end of the lumber must be lifted slightly to avoid snipe at the tailing end. (Vice versa if the first or last head is on the bottom.) I have seen unsupported lumber bouncing up and down and this bounce was transferred inside the machine and caused ripples on the lumber mid-length and snipe on the end.
From the original questioner:
Thanks to all. I think I've located the culprit – a worn infeed roller bushing block on one side.
The comments below were added after this Forum discussion was archived as a Knowledge Base article (add your comment).
Comment from contributor A:
I understand you resolved your problem (worn in-feed roller), and it sounds like you know your planer quite well but one should always remember to consider the basics of a cutter head when attempting to achieve a good finish. Correct RPM, correct number of knives, correct feed rate for the previous variables, and balance of the head, all help add to the finish quality.