Tenon Cut Quality Problems and Tooling Issues
Woodworkers trace bad cuts on tenons to defects in shaper knives. January 29, 2009
Question
I have taken the advice of some folks here and started to do my tenoning on one of our shapers rather than use our tenoner. Have a look at the linked photos and tell me if this is a typical result and/or acceptable for a new set of knives?
Forum Responses
(Solid Wood Machining Forum)
From contributor T:
What type of cutting tools are you using? Looks almost like the tools were dull or had a negative hook. Can you post a picture of the cutting tools?
From contributor H:
I have to agree. It looks more like it's tearing rather than cutting. I have cut a few tenons on a shaper before and never had anything that bad. If that was the best it was capable of, I'd make a shoulder cut on a saw first but that's not acceptable in my mind.
From the original questioner:
The top view is a brand new cutter head - just took off the coating. It is part of a series of eight designated heads for sash making. The same or worse result happens when using pine. Spindle speed is 3k rpm and the diameter of the head is 9.5 inches.
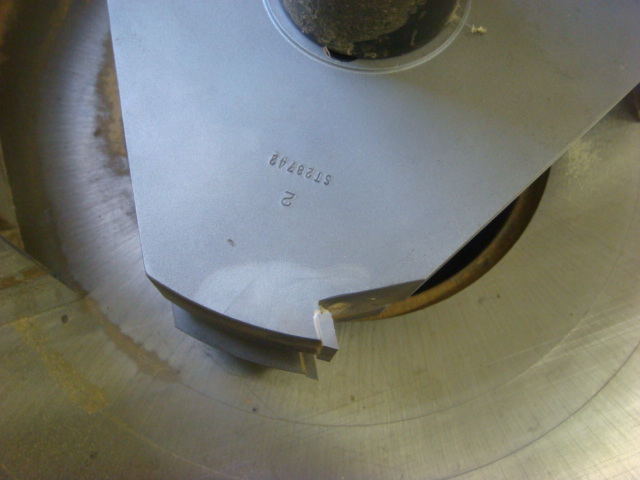
Click here for higher quality, full size image
From the original questioner:
Here is the side view.
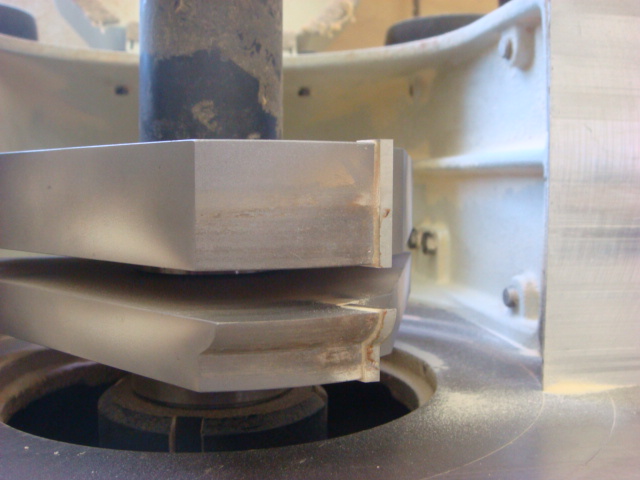
Click here for higher quality, full size image
From the original questioner:
The cutter head is a custom profile. Three winged.
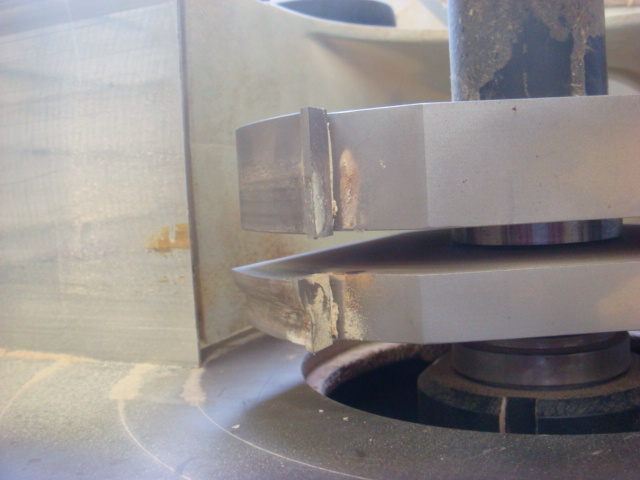
Click here for higher quality, full size image
From the original questioner:
Overview - the hook angle is 20 degrees.
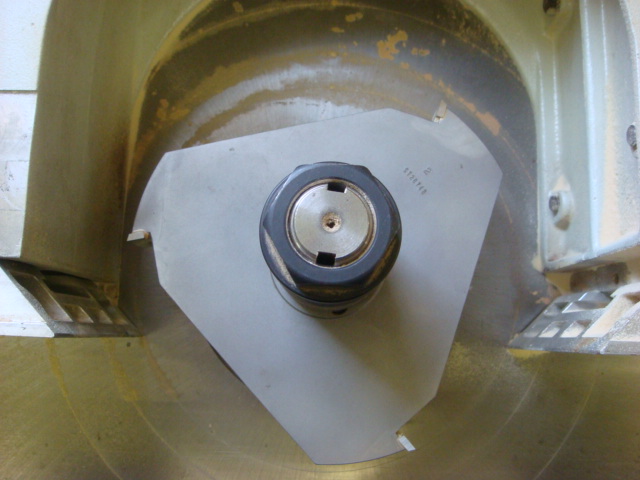
Click here for higher quality, full size image
From contributor J:
I would say those are unacceptable results. Our 250mm Garniga insert tenon sets cut perfectly and nothing like I see in your pictures. I dont know what the hook angle of my set is but the cutters are also angled in the vertical. The other difference I see is the Garniga slotting cutters have incisor knives at the edges to make a clean scribing cut. The European cutters are always stamped for the max speed and the 250mm set says 4500. With the 9 set maybe you need more RPM? I would send them back.
From contributor T:
Cutting across the grain can be a bit tricky at times. I have seen the best results with a particular configuration of tools.
6-Wing Cutters:
The outer cutters sheared to the middle.
Tantung tipped rather than carbide.
The six wings break up the cut so each tooth pulls less on the fibers of the wood.
The shears pull the surface materials into the cut so that they get cut.
The Tantung tips are sharper than carbide so they cut through the fibers easier.
Also, your RPM's should be between 3600 and 5400 for best performance.
From contributor R:
I've always had excellent result using two stacked rebate cutters with spacer between them. These cutters are form Felder which I believe are made by Leitz.
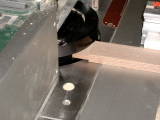
From contributor J:
I am posting pictures of some Garniga door and window tools. I hope the maker of your tools will fix them or give you a refund. They look pretty rough. As I told you before the tooling costs for doors and windows can be more than the machines they are used on. You want to pick a company experienced in this with a good track record. I think the design, engineering and balance of the head is more important than number of cutters or carbide vs. tangtung. But that is just my opinion; I am an end user not a tool maker. Most of our tools are 3 wing (Z-3) or Z-2 and they all cut fine with and across the grain. I think Z-6 is used where high feed rates are desired.
These tools are designed with all the things you need for building a quality doors and windows. Removable inserts for weather strip and weep slots, insulated glass expansion channels, dry gasket slots, removable & adjustable joint radiusing and edge breaking ECT.
If you invest in better tooling you want consider if you will go beyond your shapers in the future. Most modern tenoners, profilers and window machines are 40 or 50mm bore. Some newer machines are going to HSK 85 that almost any bore size can be used. Most of this type tooling is too heavy to use on HSK 63 CNC routers. All my shaper tools are 40mm bore and wish I had gone 50mm. Sleeves can be changed to bigger bore size and cutters bored out but it gets expensive.
The first picture is a 250mm diameter double tenon cutter for 56 to 78mm thick square edge doors. Notice the removable joint radius cutters and the scribing knives between the cutters. This one makes a clean cut across the grain, with or without the radius knives.
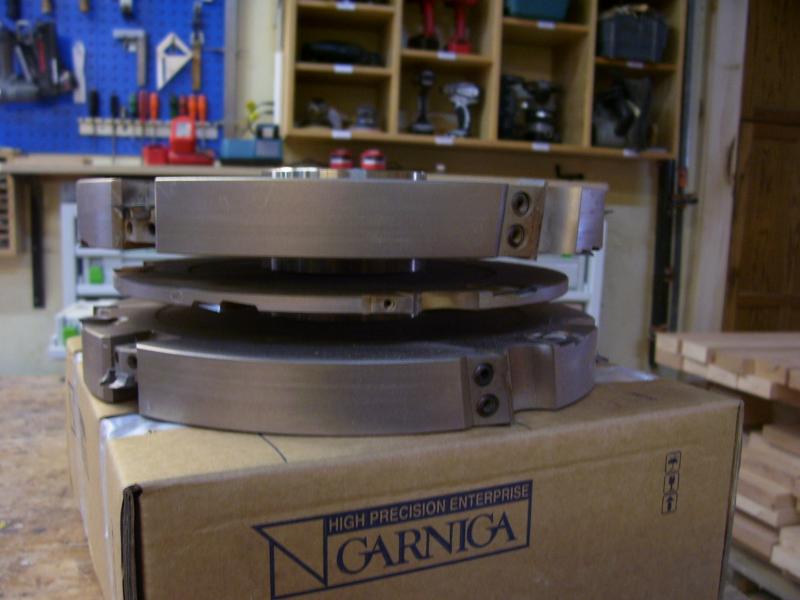
Click here for higher quality, full size image
From contributor J:
This one is our window frame coping head for dowel construction. It is 250mm diameter and weighs over 40lbs. It has edge breaking chamfer cutters and scribing knives. All the coping and tenoning tools have the same cutting circle and height built into the sleeve so the setup is the same for all cutters. The profiling tools are the same way at a smaller diameter. This gets real important if you ever go to multi-spindle profilers and tenoners.
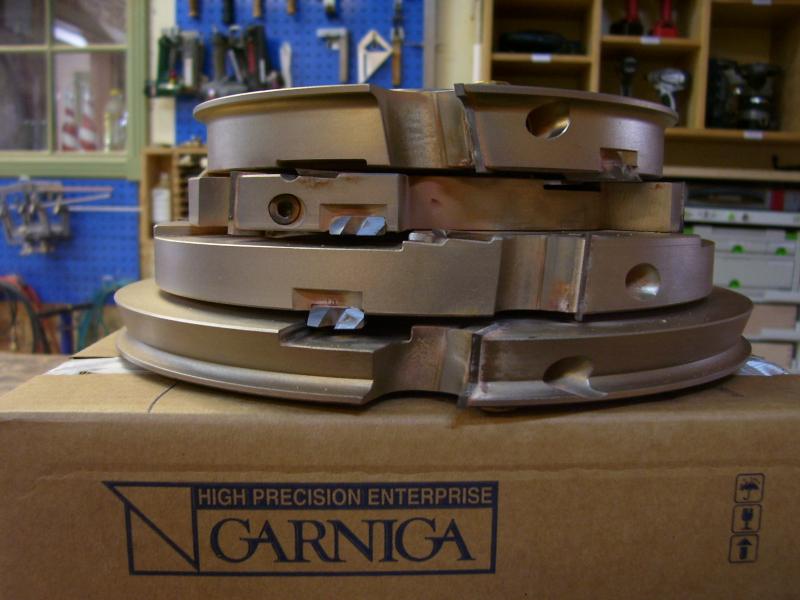
Click here for higher quality, full size image
From contributor J:
The last picture is a sash outside rebate profile. It has removable slotting cutters for gaskets. 130mm cutting circle.
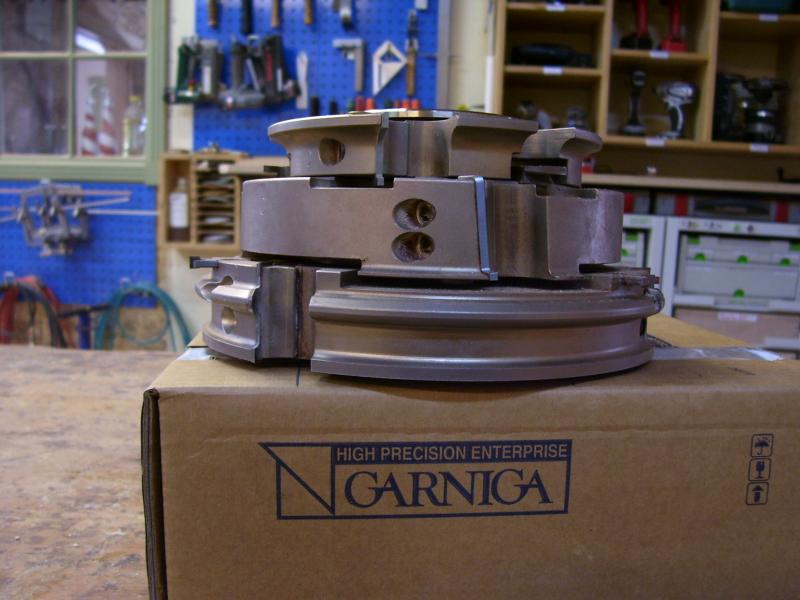
Click here for higher quality, full size image
From contributor T:
Six wing tooling is used quite frequently in coping applications of all types. It is not just for high feed applications. In insert tools, as Joe shows, diameter constraints make six wing tooling less likely but not impossible.
Now the use of Tantung over carbide is more of an application for brazed wing cutters like the ones you have shown in your first tooling pictures. The grades of carbide used for brazed on carbide teeth are typically softer and coarser grained. If you have the budget to go with insert tooling, as contributor J shows, then the solid carbide inserts get you almost the equivalent on their own. Do note that the tooling pictures that contributor J posted include shears that pull to the middle of the cutters. I do agree with contributor J that you should seek a refund on the tooling you have. Something is not quite right with something on them.