Spot Checking for Drill Hole Placement
For high-volume production work, a simple gauge is the best way to check for consistent drilled hole location accuracy. July 13, 2010
Question
We make thousands of unassembled cabinets with doors and drawers that are designed so that the customer assembles them. Since we don't assemble these cabinets, it is critical that we do quality control checks.
What is the easiest way to spot check the placement of a 3mm drilled hole center to the board edge? We are currently using digital calipers, but employees find it difficult to find the center of the hole with a caliper. We need to spot check hole center to edge as small as 0.20" and digital hole center calipers that I have seen only measure down to 0.39". I was thinking of test jigs to find the hole center to panel edge, but they can be expensive to make.
Also, what is the best way to spot check for panel sizes up to 20" with a tolerance of 0.01"?
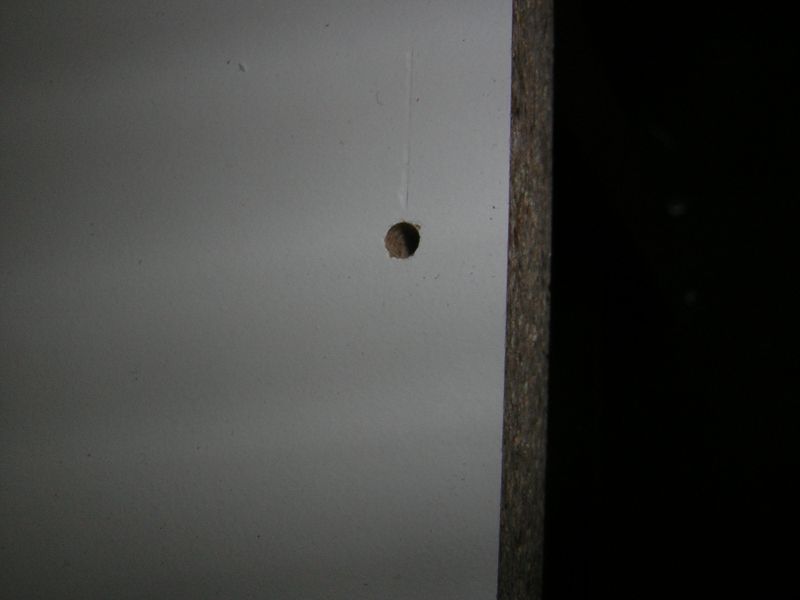
Click here for higher quality, full size image
Forum Responses
(Cabinetmaking Forum)
From contributor G:
Since the center of the hole isn't going to move away from the edge of the hole, why can't you just measure from hole edge to board edge and subtract the radius of the hole? As for the panels you need spot-checked, how many different sizes are you talking about?
From the original questioner:
I use the hole side measure method to check sometimes, but was concerned about having two measurements on the spec sheet for the same hole; this may cause mistakes when setting up the machine to drill the hole center. Unless I used the hole side measure to set up the machine for drilling.
We have 21 different panel sizes ranging from 4" to 32" (I know I said up to 20", but it is up to 32" and could be 72" in the future).
From contributor R:
We nest all our parts on a Busellato 200 RT. To check accuracy of our tooling, alignment of the head and router, and positioning of the table alignment pins, we developed a simple program. We rout a 100mm square using our perimeter routing tool. We offset it 20mm in both X and Y and drill an 8mm hole directly in the center. Starting with making sure the spoilboard is the same thickness as indicated in the corrector's column, we measure the diameter of the 100mm square. Adjust diameter and length of tool till correct. Measure from center hole to 100mm rout to check alignment of head and router. Any discrepancies, adjust numbers in aggregate correctors column. We then measure from the outside edge to the 100mm rout and check to see if it's 20mm in X and Y and adjust numbers in aggregate correctors till correct. If all these measurements are accurate, your machine is fine tuned and ready to rock.
From the original questioner:
I didn't mention that I am using a panel saw to cut these panels and we don't have a CNC router table. I am currently checking these panels for cutting accuracy with a tape measure by converting inches to mm, but the tape measures are not that accurate after a lot of use. So I'm looking for a better way for an employee to check size every 5 to 10 panels before packaging up in a box.
From contributor J:
Make a go/no-go gage (check Wikipedia for an explanation of this). No measurements needed. It either fits or it doesn't fit. These are commonly used in the manufacture of metal parts (think car parts).
From contributor N:
"a tolerance of 0.01"?"
In my opinion, you're kidding yourself if you think you can maintain that tolerance. Even if you can cut that accurately, the board will shrink and expand that much. Maybe you mean a .02" tolerance; +/-0.01"?
From contributor L:
I vote for the go-no go jigs, clearly marked and made by a machine shop. No judgment is needed - either it fits or it doesn't, and you can build in any level of accuracy you want.
From contributor C:
I would also use a go no go jig. Make at least two with a fence on the end so it automatically lines up with the edge of your panels. This is how I make my drilling jigs for hardware. You make two so after a few hundred passes you can check one against the other for accuracy.
From the original questioner:
So make a panel with a fence on one end and then place the panel to be measured up against the fence and then line up the other end of the panel with a line on the jig?
From contributor C:
I would make a jig with a fence on it and bore a through hole the correct distance from the edge. You could then line the jig up with the hole you wish to check and by inserting a proper sized dowel through it, you would know if the two are aligned properly.
From contributor B:
Thousands of unassembled cabinets? You need a CNC. Use contributor R's method for checking accuracy, get rid of a couple employees, keep the money for yourself. Failing that, add another vote to the go/no go jig method. That will be fastest and most foolproof.
From the original questioner:
I cut 4 sheets of 2 sided melamine at once on the panel saw. Then I drill 50 holes at once in the side of each panel (for shelf hangers) using a separate drilling machine. This may be faster than a CNC cutting each panel and drilling each hole separately.
From contributor S:
Nobody suggested that. A CNC can drill 10 or more holes simultaneously. And nobody building 1,000s of cabinets should be cutting them with a CNC.
From contributor A:
Metric steel rulers are more accurate than tape measures and stay accurate forever. They cost about $20 from PEC (Products Engineering). They make nice tools like squares, calipers, rulers, etc. Kind of like Starrett without the fit and finish. The cost is way lower. I've got a few small combo squares and a fist full of various rulers. I keep a 24" 4D flexible black EZ-read on the tablesaw fence.
Your measuring task should not include the math. Provide the measurer with the appropriate steel dowel as well as a written dimension from the edge of the panel to the edge of the dowel.
These dimensions would be easy to take off the CAD drawings and there is no chance of calculation errors.
From contributor B:
My bad. I thought you were cutting on a slider. I broke my own rule, RTFP - Read The Flipping Post.