Shrinkage in a Tongue-and-Groove Pine Ceiling
A discussion of all the bad things that can happen if you don't check the moisture content of wood before nailing it up.April 22, 2014
Question
I am doing a project and the owner's pine tongue and groove ceiling is shrinking. The builder now has installed extra humidifiers to increase the moisture in the home to swell the wood back into place. Being a cabinetmaker and having 30 years under my belt I know that this is a futile and damaging process. The issue is the initial MC of the material which I am sure was much too high, along with the material not being sealed on all faces. The owners are beside themselves and would like to hear from others what they should do for this. Any input would be greatly appreciated.
Forum Responses
(Cabinet and Millwork Installation Forum)
From contributor G:
The only option would be to add a small batten moulding to cover the joints or remove and replace with properly dried material. Adding to much moisture to the room is a good way to damage any woodwork that was installed with proper MC.
From the original questioner:
The batten is out of the question. The material will continue to shrink, and expose more joints. Removal is my thought and new materials stabilized and coated on all sides. I am posting this in order to show the owner what the rest of us know and believe is the proper solution.
From contributor J:
We have a tongue and groove ceiling in the living room and it expands and contracts as normal. We use a 4 1/2" crown around the edges to hide the gaps. Another thought is to finish it before it goes up. It’s much simpler and if you stain/paint the tongue you shouldn’t see any white gaps when it’s up.
From Contributor Y:
Definitely want to pre-finish, even properly sealed there will still be seasonal wood movement exposing the tongues that if aren’t finished, well, we all know what that looks like. Is there any way to get the existing off without destroying it, then properly finish and reinstall along with whatever additional product is needed? At least it wouldn't be a total waste.
From Gary Katz, forum technical advisor:
What is your relationship to the job? Why is trim out of the question? In most parts of the country, some type of trim is a necessity, especially on materials applied to a ceiling, where the heat rises and the air dries out more than anywhere else in a home. There could be many reasons why the ceiling is shrinking. Knowing the MC of the wood before it was installed would solve the question. Knowing exactly how much the wood has shrunk, and what the MC is right now, would help, too.
From contributor G:
Sealing the wood on all sides will slow the expansion and contraction due to gain and loss of transient moisture. If the wood is at 14% green MC when installed it will shrink. In this situation a board and batten instead of tongue and groove would look better. The lumber needs to be 6 to 8% then there will be no issues with exposed tongues.
From the original questioner:
My relationship is that I am installing the doors, baseboard trim and window trim and have cabinets for the closets. The home owner has asked my opinion regarding the issue and I have pretty much said the same thing that everyone is saying.
I am positive that the moisture was never checked and the materials were never allowed to stabilize, along with only the exposed face being finished after install. This is an area of about 3,500 square feet of ceiling, lofted, etc. Trim on the perimeter at the walls etc. is installed. The main concern I have now is that if I go back and install more casing with the humidifiers running full blast and no control once everything dries out the trim will shrink and I will be on the hook to repair. There are just so many scary scenarios with the moisture being added that I am going to tell the home owner and the builder that I will not install anything until all systems are up and running and that the MC is under control and has had four weeks to balance out. Any thoughts?
From the original questioner:
Here are a few pictures to show the job.
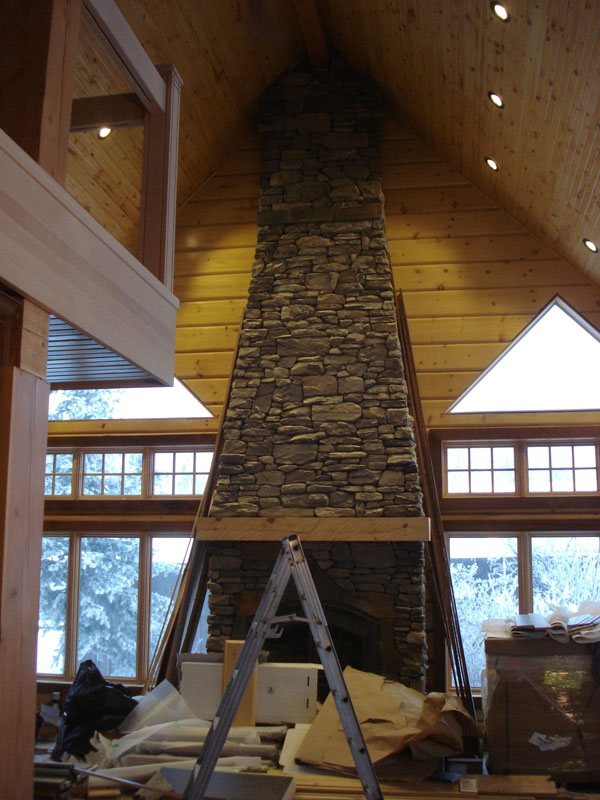
Click here for higher quality, full size image
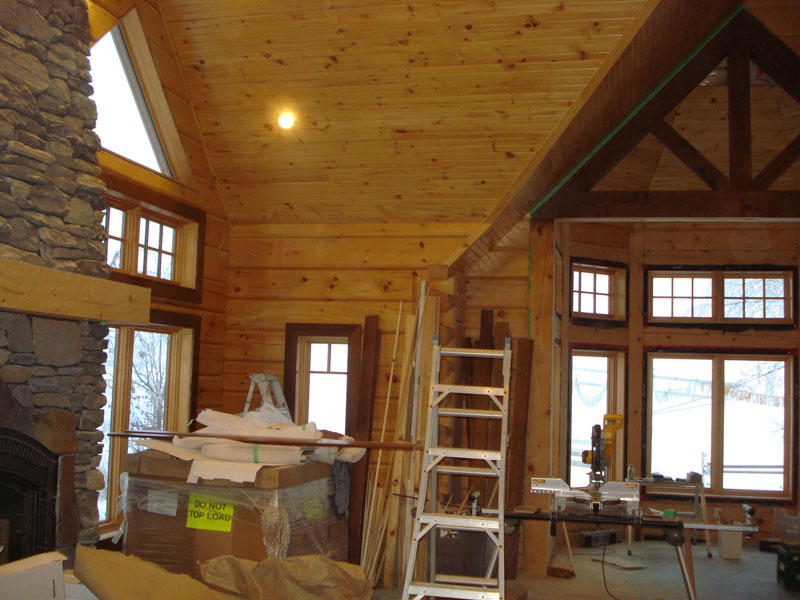
Click here for higher quality, full size image
From the original questioner:
On a side note, the tongues have come completely out of the groove and there is about 1/2" between them and things are still shrinking.
From Contributor Y:
Agreed. I wouldn't install any more trim until they get the humidity stabilized and the current issue resolved. From your pics would I be correct in assuming that even if your trim was not affected it would still have to be removed if the builder ends up having to replace all the tongue and groove?
From Contributor Y:
"On a side note, the tongues have come completely out of the groove and there is about 1/2" between them and things are still shrinking. " A humidifier isn’t going to swell them back. Was this product green when it was put up? That’s a lot of movement. 1/4" would be a lot on an 8" board if it were kd. It sounds to me that the builder is just trying to stave off the inevitable.
From Gary Katz, forum technical advisor:
Sometimes someone is so right that there's no reason to say more. Contributor Y hit the nail on the head. Beautiful job – it’s too bad. I visited a job last year where the finish contractor installed miles of tongue and groove. They did a beautiful job of installation - nearly all the walls and ceilings in a celebrity home. It was all painted and finished when I walked through. The contractor was complaining about shrinkage - the boards were separating about 1/16 to 1/8 inch (larger gaps higher on the walls and across the ceilings, still fairly tight near the floor) and the painters were having to caulk every one – every one. He said the material was defective and the material supplier should pay for the cost of caulking the joints.
I measured the MC of the boards. Near the floor it averaged 13%. Near the ceiling it was around 10%. I suspected, since the gaps were around 1/8 in. on the ceilings and high on the walls, that the original MC of the 1/6 boards had been around 15% or so. Eventually everything would stabilize around 8%. I suggested they stop caulking. That was like peeing into the wind. It all blew back on me. Or so they thought. I haven't heard what happened, but I don't need to. As the boards continued to shrink, with the caulking between them, especially the ones lower on the walls, they must have split and cracked, too. I suspect they re-caulked and repainted, at least a couple times. Obviously the material was too wet to install in the first place. But no one checked it. These days, knowing the MC before installation is the responsibility of the finish carpenters - period. For every 4% change in moisture content, flat-grain softwood will change size 1%.
From Contributor C:
Last winter I installed a tongue and groove house like this as well as the doors, baseboard trim and window trim. The builder pushed and pushed. They didn't really care about the MC and we had extremely cold weather. The wood was still green and packed in plastic. He didn't even want us to use glue on the ceilings to help lock it in but we wouldn't give on that. Good thing was winter is generally drier. Bad thing was this builder shouldn't be building this house. We made him sign a release because we couldn't warranty the installation because the house wasn't conditioned during installation. We used 1" x 2" trim along the ceilings that were vaulted and 1" x 4" on the flat ceilings. They sprayed clear coat in the house which sealed in real nicely and helped. There isn't much you can do without replacing the tongue and groove or covering. I would prefer replacing just to maintain the look.
From Contributor Z:
Seems like a 20' plus ceiling height. Adding too much humidity could actually cause rain on the inside of the building. This occurs a lot in barns with fresh hay unless there is a sufficient way of venting the humidity. I would suggest that they stop the extra humidification unless the Relative Humidity is below 30%. With this ceiling height the climate (humidity and temperature) changes throughout the space. What kind of heating system is running, forced air or radiant underfloor?
To get a steady shrinkage rate you need to run fans to circulate the air both vertically and horizontally. There are methods of removing sections of the tongue and groove - clamping to squeeze them together and patching the sections that are removed similar to wood flooring repairs. This takes a bit of time and trial and error. It would be less expensive to remove and reinstall once the tongue and groove has stabilized. Things will change in the summer especially if the space is air conditioned. The exact opposite will occur and if too tight there will be severe buckling. As I indicated earlier circulating conditioned air throughout the space is critical with this amount of woodwork on every surface and this has to happen with every season. Heating Ventilation and Air Conditioning should be tuned via the control system to moderate humidity for the next three months then adjusted again as the moisture drops in the wood. Sealing all edges reduces this issue but does not eliminate it. There are a lot of issues affecting the wood moisture, how close is the bathroom, kitchen. If the heating system is forced air is there a humidifier installed. Ceiling fans are not noticeable but would help.
From Contributor S:
I would have to say the humidifiers need to go, then re-install with the backs sealed. I have used shellac successfully and it is quick and easy. The balance issue is the same we see in furniture and cabinets. Of course if the material were quarter-sawn it would move roughly half as much depending on the species. As to removing without damage, I'd say side cutters to clip nails or end nippers to roll the nails out. Experiment by the hour!
From contributor K:
This material is one of the cheapest wood products out there. You could tear it down and start over. I am going to suggest leaving the faulty material in place and not spending the money or time to remove it. It will serve as insulation and the new material can be installed correctly as an overlay. Tough lesson and this is going to evaporate someone’s income/profit. They should have known better. I expect they will be held accountable? If they were working cheap, the general contractor got the hack work he/she paid for.
From the original questioner:
I have let the owner see all the comments, and informed him that I will not install any trim, etc. until the humidity is under control and stable. The builder got someone else to finish the trim, etc. which is no big deal to me. I do not want to get into an issue later so I feel that it is better to step back from all this. I have cabinets that I made and will be installing in the next week or so which have been finished on all sides before assembly so I am fairly confident that any moisture fluctuation will be nominal on the cabinets. I’m going to change my contract to specify controlled stable humidity, even though I have a clause that states changes in humidity are not our responsibility if anything happens.
From Contributor Y:
Good move on your part. Even though it stinks to give up a job in this economy sometimes it’s better to take the short term loss to avoid the massive migraine coming down the pike later. I have been fortunate in that I have never needed a contract with my customers and have been able to do things on a handshake. Only once was I called back for a trim nightmare. It was a house I finished over the summer several years back. The house sat until winter when they finally got the mechanicals working. The plumber’s helper was in the attic on a Friday in February and it was about 12 degrees out. He was hooking up the a/c units and since it was cold he jacked the furnace up to 90 and left the scuttles open while he worked. Well, quitting time arrived and he want home. He left the scuttles open and the heat up to 90. The house sat that way for another week before anyone came by. Basically the house turned into a kiln. Every newel post on my stairs was split right up the middle. The walls shrunk about a quarter of an inch - you could have dropped a piece of quarter inch plywood between my stairs and the wall. The baseboard shrunk up off the floor almost 3/8 of an inch, the crown was blown clean away from the ceiling, and every miter on every window and door could have had a cat thrown through the gaps. Even the oak floor had 1/8 to 3/16 gaps. Unfortunately for the builder it was the new homeowner that discovered it. I just wanted to scream when I saw it. After asking me what could be done he said "don’t you warranty your work for a year?" Fortunately he and I had a good working relationship and he didn’t push it knowing it wasn’t my fault.