Quirk Bead Cutters
An extended discussion on cutterheads for making quirk bead, plus equipment choices and setups for this custom decorative detail. March 3, 2009
Question
Anybody know a source for an off-the-shelf 3 wing carbide shaper knife with a beaded face frame profile? I am looking for a .25" diameter bead with a 1/16" groove for a total of 5/16" from the edge. If not... what's your favorite 1/2" shank router bit for the same purpose?
Forum Responses
(Cabinetmaking Forum)
From contributor A:
They don't exist. I had my custom knife grinder grind me a pair of knives. They are about 2/12" tall with staggered bead profiles. 1/8" R, 3/16 R, 1/4 R. They have the typical 1/16 groover with each radius. It looks like 3 router bits connected to each other. The bead burns (cherry) much less on the shaper with sharp steel than a carbide router bit.
From contributor J:
Yup, same as contributor A. I started out using a router bit, but not really practical for running a kitchen's worth of parts. Then I bought an off-the-shelf cutter and was not happy with the profile. So the next step was to come here and ask, like you're doing, and the guys said go get yourself a custom cutter made. Well, that's what I did and I have to say it wasn't that expensive and it did exactly what I needed it to do. I went with a 3 wing carbide tipped cutter since I didn't need any other beads.
From contributor C:
LRH (maker of Magic Molder) has a Magic shaper head. One of their newer plugs has the detail you describe.
From contributor A:
Contributor C might have the right idea. If you are running a 3/4" spindle the head is $107 and the pair of cutters is $99. A pair of custom steel knives will cost at least $100. I picked up a CMT insert head a few years ago. I can get custom knives cut for that for about $85. If I needed a quirk cutter now, that's how I would do it.
From contributor T:
We use the LRH insert that contributor C recommends. It works great.
From the original questioner:
Guys... just found this by searching for "Quirk Bead" instead of "Edge Bead" like the router bit makers call them. Freeborn is making 3 wing carbide shaper knives in four different quirked bead sizes! It is $87.00... Not bad. How are you shaper users setting your power feeds up for edge profiling face frame stock? With the Magic Molder, it would be easy to use my saw feeder with the stock face down.
From the original questioner:
Just noticed you guys are talking about a shaper Magic Molder and not a table saw Magic Molder. Same question... power feed on the narrow edge?
From contributor J:
I set up my power feed to push against the shaper fence so it's got the most contact with the work piece. If you go the tablesaw route you would push down on the TS top. Funny thing is I have the Magic Molder set up for my tablesaw and have never used it. Just always seems more practical for me to set up a shaper than take a saw offline for a run. Once I get a shaper set up, I leave it for the duration of the job. Then it's ready for those pieces that got missed, or mis-cut for that matter.
From the original questioner:
Yeah... I have two saws but I guess I need another shaper because I have frame and panel to run on the same job as the frame stock.
From contributor J:
Of course you need another - that's never a question! I have 2 cabinet saws, 2 shapers, 2 jointers, 2 planers, 2 (oh wait, make that 3) drill presses, etc, etc, etc. You always need another, now I just need a bigger shop!
From contributor U:
I make a zero clearance shaper fence that clamps on over the stock fence for moulding like this. Then the feeder runs pushing the stock against the continuous fence. I would run the bead on the bottom - more area for the feeder wheels to push on above the cut.
From the original questioner:
Oh yeah, for sure the shaper elevation will be set to have the outside edge of the quirk machined at .3125" above the shaper table surface. That way, any width of face frame member can be run with only one elevation setup. It's just that I have never set my powerfeeder to run the stock between the wheels and the vertical surface of a fence. Only between the wheels and the horizontal surface of a table. I have the Delta 36-850.
From contributor P:
I see the cut on the face frame with stock, but what about when a stile and rail meet?
From the original questioner:
Those cuts are done without a shaper. Everyone has a different method and there are even dedicated haunching machines sold for the purpose. The tools I use are the table saw, bandsaw, chopsaw, flush trim bit in a table and a sharp chisel. The chop saw and its jig are used only for the end grain half of the joint.
From contributor R:
If it were me, I'd run the stock through my Woodmaster. Their designer knife #DS 1 is the profile you want. The advantage to the Woodmaster is that the setup is simple, powerfeed is not only included, but infinitely variable 0-16 feet per minute, and the same machine can gang rip the stock should you need to. With the proper setup, it can do any width stick up to the machine's width. A Williams & Hussey molder can do it too.
Lastly, the cheapest way out (if you won't be doing this all the time) is to mount a power feed to your table saw, and buy a molder head for the saw. You can get a brand new Craftsman unit with knives for about $80.00 last time I looked. Just a few other options. Almost any shop job can be done more than one way. Which is best for you is dependant on your shop setup and needs.
From the original questioner:
I have an RBI planer style molder and I grind my own knives by hand and eye and use this machine constantly. However... just to talk shop with you, I would not choose a planer style molder for this particular job. The main reason is because I am dealing with multiple widths of face frame stock. I think I have 6 or 7 different widths. With the planer/molder, you need to alter the bed guides for every differing width.
With the shaper, one setup will work for all my different face frame stock widths because the elevation of the profile is indexed off the shaper table and the power feed will also stay in one fixed position. This will save me time especially when something was forgotten or a mistake is made and more stock needs to be run, etc.
The secondary reason is that I like to climb cut this profile due to the nature of grooves to tear out. This is why the stick and cope makers have all gone to a rounded edge on the panel face side of the panel groove.
From contributor R:
Not to argue, but I know the Woodmaster or the RBI can do this cut since I've done them. The trick is to ensure that the part is oriented properly so that the grain runs up and toward the infeed as you feed the parts.
As for the varying widths, you can use only one guide. Set the guide on the bead side, and angle it just a little so that the feed rollers will push the part against the fence. (Just like angling the power feeder toward the shaper fence.) You only need a very small angle.
I helped a client set up a Woodmaster to make stair nosings like this. The round-over was set to one edge, and flat knives across the rest of the bed of the 12" machine. Made it easy for them to run any width from 3" to 12".
I'm not insisting that you need to do things my way! I just wanted to answer your issues. Any excuse to buy another tool can't be all bad!
From contributor B:
You probably need a custom corrugated knife made for that to get the right quirk. As far as running it on edge, that is easy. A lot of times the power feeder is not too cooperative running a 3/4" piece on edge, so depending on how many feet you need, use some 2 sided tape and put 2 pieces together, giving you 1-1/2. Also I use a second fence that has a slight radius to force the piece against the knife, and using the power feeder I run the stock between the shaper fence and the auxiliary one.
Check out Oella saw and tool out of Maryland. Dave Hicks has helped me a lot with knives that I have needed. He is fast and his quality is excellent.
From the original questioner:
Angling the bed guide even a little from 90 degrees to the shaft will change the profile. With beaded face frames, I need an exact .3125" wide profile in order for my cut lists to work. The rail lengths depend on the quirk and bead totaling exactly .3125".
As far as grain direction, many of the parts in beaded frames need to be run on both edges. That means going against the grain on one edge in the planer/molder.
Lastly, groove tear out happens while running parts with the grain and against the grain. It is not a grain direction problem but more of a "ripping without a zero clearance insert type problem." Hope that makes sense.
From the original questioner:
Contributor B, I think you missed my post above - Freeborn is making 3 wing carbide shaper knives in four different quirked bead sizes! Only $87.00 each.
As far as the other, I would use a feather board instead of 2 sided tape I think. Besides, people seem to be saying that most power feeds can be oriented to have the wide face of the stock sandwiched between the feed wheels and the vertical fence surface.
From contributor B:
Can you flip the knife and stock and run it backwards when you have the grain change? I have had success with that in some situations.
From the original questioner:
Well, to climb cut, you don't flip the knife, you just feed the stock in the direction of the cutter's rotation. This can only be done with a power feed on a shaper. By hand you will... well... come up shorthanded. You cannot climb cut on any planer stile molder that I know of.
From contributor B:
Yeah, I missed that one. That's a great deal!
I know what you mean about turning the power feeder to hold the stock against the fence. I have a big 4 wheel Delta. Real pain in the neck to try and spin that sideways - that is why I use the other method. The reason for the doubling of the stock is for the feeder to have more area to grab. Otherwise the feather board is just as good as the auxiliary fence.
From the original questioner:
I am curious about flipping cutters or knives backwards or upside down. Seems to me if you do that, you would have to change the cutter rotation direction to avoid the backs of the profiles slamming into the wood instead of the cutting edge?
From contributor C:
The 041 Freeborn shaper cutter you mention should work fine. I have a similar 3 wing cutter made by LRH years ago and it's 95% tear free running conventional rotation. Freeborn makes a better braised cutter in my opinion. We also run these on the moulder using width adjustable insert cutters with no tear out. You need to be removing material from the flat surface at the same time to get tear free on moulders. I have a LRH Magic Moulder shaper head for some other profiles. I don’t know if I got a bad one, but it’s difficult to change the plugs on ours.
We used to turn the feeder against the fence for this but discovered we could just use the feeder in the normal position on the edge of the board and use Aigner pressure rollers to keep the stock face tight against the fence. It’s not a big cut so not much pressure back. The only down side to this is you have to raise and lower the feeder for different widths. This is quicker than turning the feeder unless you have a Wegoma feeder.
From contributor B:
What I meant by flipping the knife was to run it in the other direction. Turn the knife over and reverse the motor. Not to run it backwards, as I think my wording described. And yes, only with a power feeder to climb cut. Sometimes but not always it works as an alternative to climb cutting. ("Shorthanded" puts it mildly, not to mention the Phoenix missile launch in your shop when the wood catches on the knife!)
From contributor J:
Ease of changing the feeder position greatly depends on the feeder itself and how the motor is oriented on it. I have a Delta 1hp 4 wheeler that's a real pain to set up. It's just slow and cumbersome to rotate it that 90 degrees to feed against the fence.
On the other hand I have a Univer that's much quicker. Most of the difference is in how the motors are positioned on the feeders. On the Delta it just seems to be in the way whenever I'm rotating it. With the Univer it's usually not as much a problem.
Also I had a posting a while back concerning climb cutting with my S&R profiles. I remember at least one person saying that climb cutting would wear the cutters much faster, I believe because of the way it scrapes instead of cuts. Anyway, I took some advice and went with the Freeborn sets and had much better results taking a regular cut (although I also switched to a 1-1/4" spindle for a larger cutting diameter). Since you're looking at Freeborn cutters anyway, I would try taking a normal cut before setting it up for a climb cut.
From contributor A:
Get the Freeborn cutter before I try to corner the market. It's about time somebody woke up and started offering that profile. For $87 you would have to be a dope to do this any other way. It is much easier to run small pieces on the shaper with the power feed than the RBI/Woodmaster. With 3 wing carbide you will get very nice cuts. I wonder if they will break my last $100 for that Freeborn cutter?
From contributor C:
Contributor J, what side do you have your Univer mounted on? Mine used to be on the left side and was easy to turn. We added a power arm to our shaper that requires mounting on the right side control post. It can still be turned but with some difficulty. It is the position of the motor to the mounting bracket that causes the problem.
A nice feeder for custom applications is the Wegoma. It turns to the fence by a twisting motion that takes less than 10 seconds to do. The feed wheels are split with the outer half removable. This would be nice for the times you need to get close to the cutter.
Below is a picture of our shaper bead setup. Feeder is swung away for clarity. Feeder on top works for stock up to about 6 inches wide.
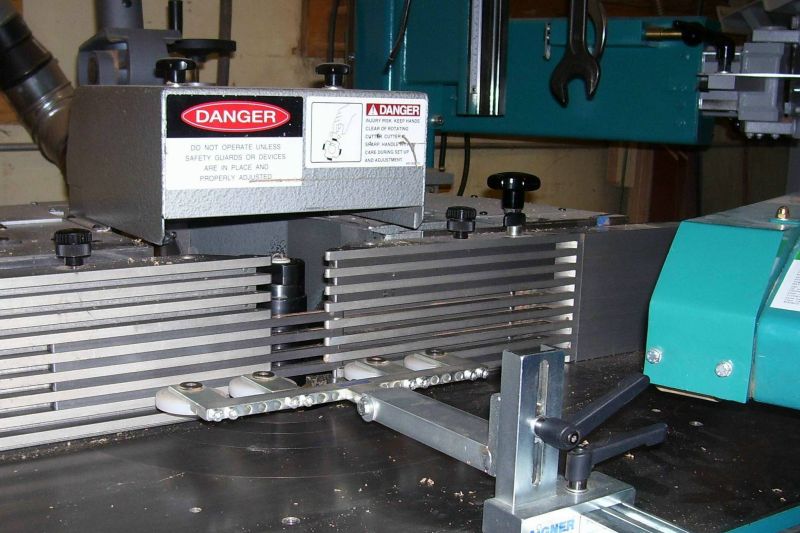
Click here for higher quality, full size image
From the original questioner:
Just FYI - the $87.00 price is 3/4" bore only. I just ordered the 1.25" bore from W.Moore for $102.00 plus shipping and drop ship from Freeborn today. I agree that it should work great and beat the heck out of the router table.
From the original questioner:
Yeah, as far as the RBI/Woodmaster... Without constant end butting, you will get snipe, and unlike contributor R's 11" wide stair treads, 1.5" wide frame members run without being captured between two fences sounds like trouble to me.
From contributor J:
I have the Univer mounted to the right side of the shaper and it's not too bad to rotate. Certainly more than 10 seconds, though. The Delta is mounted to the left side but it's more the orientation of the motor I think than the side, although I haven't tried switching the sides. With the Delta the motor is perpendicular to the feeder body whereas the Univer is inline with it.
Those Wegoma (never even heard of them before) feeders sound very cool, but at those prices I think I'd just buy several more used feeders and have 2 on each shaper, 1 set up for flat stock and 1 set up for against the fence. Okay, maybe that's a bit too much...
From contributor C:
The Wegoma feeders are for sure marketed toward the serious craftsman. Martin Germany has them on their shapers at the Euro shows. I have looked them over close and they are nice. They are actually made in the East. Grizzly has what I am sure is the same feeder in their catalogue. It’s hard to tell if theirs has the split wheel. I think the problem with turning my Univer is the angle the Martin power arm puts the tube compared to when it comes from the back of the shaper.