Quick-Release Mounting Rigs for Power Feeders
Ideas for attaching power feeders to machines so that the power feeders can be quickly mounted and dismounted. January 29, 2009
Question
I have a Delta unisaw that I would like to set up with a power feeder. Does anyone have any good ideas on how to create a quick release attachment? I’m not looking forward to bolting on and off. Also my cast iron wings are not pre-drilled. Are there any tips on drilling and tapping ?
Forum Responses
(Solid Wood Machining Forum)
From contributor D:
I have a couple of the baby Steff feeders. I mounted them on a piece of 2x2 angle bolted to the fence. When you don’t need it swing it backwards over the clamp and it balances itself. It slides along with the fence. We have three saws set up this way and never take them off.
From contributor A:
A quick release feature would be great. However, in order to withstand the forces and weight of the powerfeeder this quick release is conceivably doable, but at a high cost. Are we talking a typical 1hp feeder or one of those little guys?
A heavy duty T-Track might work but a ton of time will be spent letting it into the table. You will still have to get a wrench or socket and unbolt it. Another option would be to get a piece of 3/8" steel or aluminum plate a couple of inches wider than the base plate of the feeder. Drill and tap the plate. Then permanently screw it to the bottom of the outfeed table. This way you are just bolting into the table rather than fumbling around with bolts, nuts, and washers. I would not trust the threaded inserts.
From contributor J:
Someone on here posted a method that I thought was very clever. They fabricated a steel post which bolted to the floor next to the TS and then the power feeder would attach to the post when needed. Not sure if it's in the archives but would be worth a look.
One of the main reasons I like it is because the wings on a Uni are pretty thin and I don't like the idea of mounting a heavy (1 hp) feeder to them. I know guys do it successfully, but when I called Delta and talked to their engineers they said nope bad idea. Those feeders put a lot of leveraged torque onto the surface they're attached to.
From contributor J:
For the pain in the neck that this is going to be to rig this removable feeder up I would suggest that you just buy a second used saw and permanently mount the feeder to it.
I have a feeder on my Felder machine that just flips and pivots out of the way, and even that takes time to setup. You also need to make sure that you have your fence well supported so you don't get any flex with the pressure of the feeder. Drilling and tapping the cast iron top on the saw for the bolt holes is easy.
From contributor D:
When I mounted a feeder on a t-saw, I built a small platform the size of the cast feeder base and mounted on the back of the saw cabinet so the top of the base was just below the tabletop. The saw cabinet was reinforced with 3/4 ply to handle this additional weight.
With the base mounted below the tabletop, the feeder could crank it's vertical post out of the socket base, and then be "driven" along the catch tables to an out of the way location for ripping wide panels. No tools were required and it took about four minutes. A later improvement was to mount the base platform with heavy hinges and a bolt catch so the whole feeder assembly could be swung back about 180 degrees so the feeder would rest on the floor.
From contributor G:
I, like contributor J have a Felder (saw/shaper) with their flip down bracket. I liked it so much I bought a second bracket and with some effort mounted it to my Powermatic saw. The bracket was over $200 and worth every penny. I have not seen anything at all that would work.
From contributor T:
I also have a power feeder on the flip-down bracket (mine is a Hammer) attached to my Minimax combination machine. I had to make an angled bracket to get the right attachment angle on the vertical side of the machine to work with my shaper. But the bracket is stout enough to work as it was designed to. Bear in mind that "flipping" the feeder up and down (assuming a 3 or 4 roll feeder; mine is 3 roll) takes a lot of strength, because coming up, it's a dead lift, and it must be close to 100# for a 4-wheel. If you were to lose it at any point it would be a little catastrophe at best, or possibly break your foot if you were unlucky. I don't see why you couldn't drill slightly oversize and bolt with nuts and lock washers.
From contributor H:
I hung mine from the ceiling and it seems to work great.
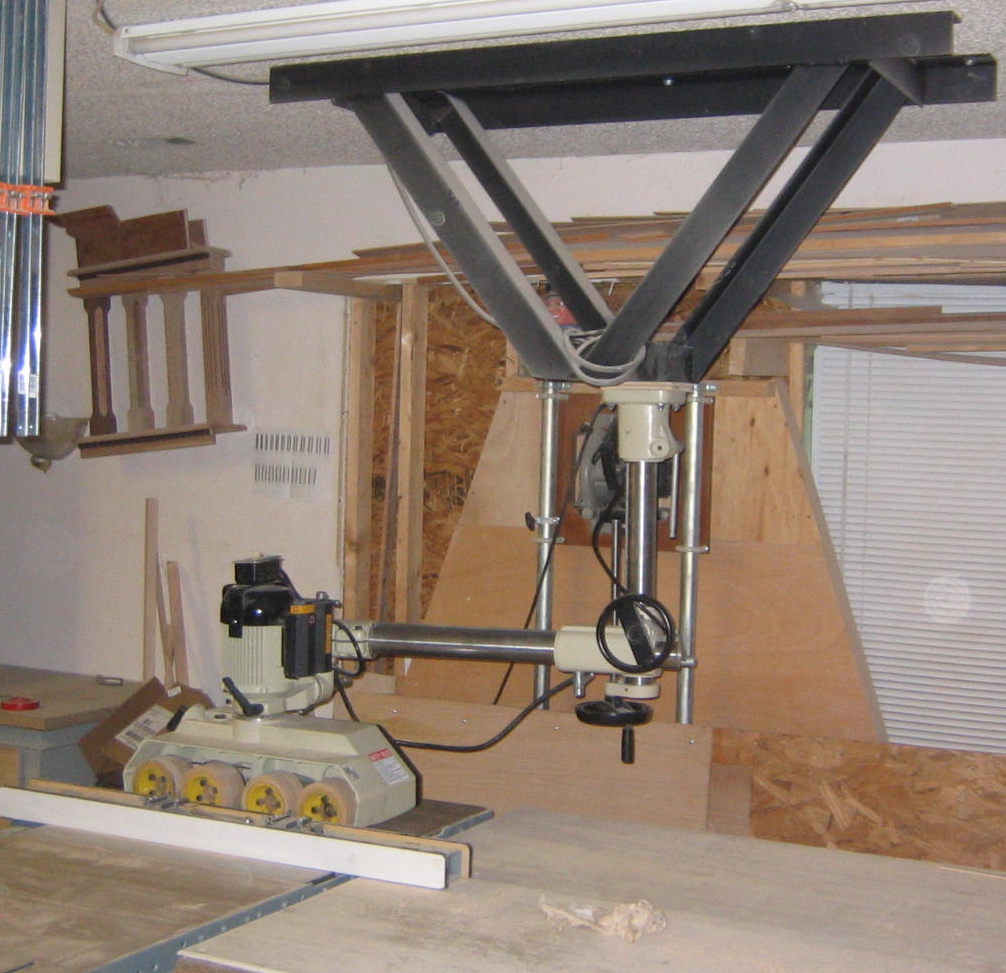
Click here for full size image
From contributor A:
I'm wondering what you guys are feeding through a tablesaw that would require a four roller 1hp feeder. I would think that you would be able to get away with a little 3 roller 1/4 hp Delta (not the fake 1/8hp).
From contributor K:
I have several stock feeders mounted to a table saws. Best way for me was to mount the cup upside down under the table top. Drill and tap table for bolts then cut hole the size of shaft through table top. I also built a leg under the cup and welded this to the cup with a wheel on the bottom of the leg (all my tools are on wheels with few exceptions, even those weighting over 12,000 lbs all have stabilizing locking feet). All you have to do is tighten the cup bolt to lock and loosen to remove the arm. The leg top welded with plate prevents the stock feeder from falling down.
An alternate method is to mount an L/bracket drill and taped to the table top, off of the rear with a leg bellow table top surface. You will have to typically extend arm or riser but this is easy enough. Buy tube steel for inside diameter and tub steel for outside diameter and drive together and put set screws in old part and new part.