Post-Forming Laminate in Three Dimensions
You can't bend laminate to around a compound curved substrate, but there are other specialized materials that will do it. December 1, 2010
Question
I would like some advice regarding post formed plastic laminate edges. I am being told by a local woodworker that post formed edges cannot be fabricated when radiused corners are involved. The edge detail I would like to use is a cushion edge that, when in use as a work surface, will not cut into the forearms of the person at the station.
Forum Responses
(Cabinet and Millwork Installation Forum)
From contributor B:
He's right, you can't post form laminate around a corner. Think of wrapping tape around a baseball. You can't bend laminate two ways at the same time. Can't be done and it all lay flat. You can segment the top, but that requires assembled joints.
You might try a heavy duty bumper T-mold around the radius. That's what most of the larger office furniture suppliers have available. You can also use solid surface and wood edges with plastic laminate tops and radius them to get your cushion edge.
From the original questioner:
Please explain to me how this was accomplished. This is Kimball's Cetra systems furnishings with a reverse knife edge that is rounded at the end. These are 12" diameter work surfaces, and out of p-lam. I am struggling with this, since most of my major systems manufacturers are now offering these edges, and these are radiused tops.
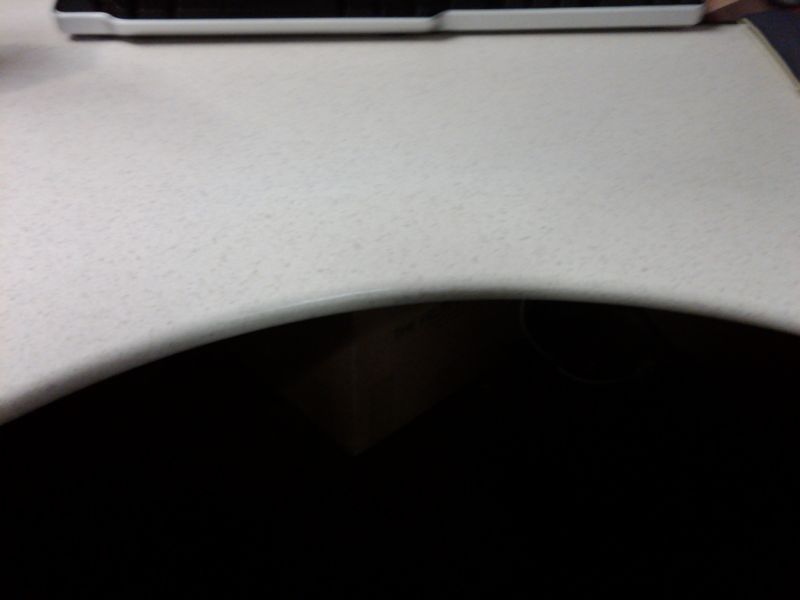
Click here for higher quality, full size image
From contributor J:
Are you sure it's not Thermofoil?
From contributor B:
I don't know how they do it. Laminate comes in sheets. How can you form a sheet in two different directions at the same time? I visited the Kimball website and it shows a footprint top that has a rolled edge around a radius as you show. I was unable to find the specs on the tops that are postformed and they don't advertise it a lot on the site either. Makes me wonder. They show painted work surfaces on the Cetra page as available, but don't show laminate as an option. But they show it on other lines as available. I'm stumped, but I'd love to know.
From the original questioner:
How comparable do you think a Thermofoil top would be to a HPDL top that was post formed as far as durability?
From contributor D:
In most instances Thermofoil is not nearly as durable as HPL. The product you see in the picture is likely one called Kydex. It is a heavy duty Thermofoil applied with a press like Thermofoil.
From contributor M:
Are you sure that it is HPL? Maybe SS or Corian like product?
From the original questioner:
Absolutely - the picture is of my desk.
So you're telling me that vinyl/acrylic can be thermoformed over a particleboard or MDF core? I use vinyl/acrylic everyday in health care design, but at a .060" thickness as wall cladding, hand rail covers, or corner guards. The alternate manufacturers are Construction Specialties, and InPro Corporation. Kydex is bid as an equal in those situations. I have always understood that Thermofoils were the paper, and topcoat before it is applied to a phenolic backer. Is that correct or have I been mislead?
From contributor M:
After looking at the KYDEX web site, I would agree with contributor D. It looks to me that would be the answer. I don't think you can get this kind of radius with laminate.
From contributor B:
Foils are paper, not laminated to a phenolic backer as in high pressure laminate. They have some wear resistance and chemical resistance but not the impact resistance that HPL has. Some foils are impregnated with melamine resin to enhance chemical and wear resistance, so I would assume if your counter is a foil, it has been treated. Some people call thermoset melamine "foil." They claim wear characteristics are similar to .020 grade HPL liner.
If it is laminate, I still can't figure out how they bend it two ways at the same time. It's got to be some sort of thermoforming process. Think I'll try to find a Kimball dealer and go have a look.
From contributor B:
From the Kydex website:
"Membrane Pressing of Routed Wood-Core Substrates allows 3-Dimensional Design Freedom.
Membrane pressing enables KYDEX® sheet to conform to all top and side surfaces of flat and routed wood-core substrates, including compound curves, sharp edges and fine details—even logos, trademarks and other corporate identity routed into the substrate. The outstanding formability of KYDEX® sheet enables it to conform fully to the core, preserving sharp edges and surface detail, while maintaining uniform wall thickness on high spots, low spots, and sharp corners where other sheet products may "thin out."
The ability to conform to virtually any 3-dimensional shape overcomes 2-dimensional design constraints imposed by high-pressure laminates and wood veneers, freeing designers to create high-style exhibits and displays that command greater attention and enhance the items on display.
In addition, membrane pressed KYDEX® sheet encapsulates all but the bottom core surface (which can be laminated and heat welded at bottom edges for total encapsulation), eliminating unsightly seams that tend to separate and collect dirt, and when safety is a concern, allowing rounded corners and edges not possible with flat-laminated materials."
From the original questioner:
Could you in fact thermoform a vinyl/acrylic sheet at its thinnest gauge .040" over a pre-formed core? What would be the best core material - MDF, plywood, or particleboard?
From contributor D:
Most likely MDF! It is available in a variety of thicknesses so you do not have to build the underside to the desired thickness.
From the original questioner:
Would you have to worry about moisture issues?
From contributor B:
If concerned, there are a number of water resistant MDF brands available. Sierra Pine has one called Medex which is also a non-urea formaldehyde product. I think MDF or particleboard would be a viable core material.
From contributor G:
This is thermoformed. Kydex is molded to a shape or over MDF to give these complex 3D surfaces. I've thermoformed parts for the cabinet industry to save time in cementing and trimming of tough areas. It comes in handy during high volume runs where I can save a store fixture company hours of labor on each display. Dow at one time also carried a product called DKE (Dow Kydex Equivalent).
On a side note, these edges can also be produced in urethane using a fairly simple injection molding process. Big runs are needed, however, and it's a big mess.
From contributor I:
This from Wikipedia:
"Kydex is a line of thermoplastic acrylic-polyvinyl chloride alloy sheet grades. It is frequently used as an alternative to leather in the production of firearm holsters and sheaths for knives. KYDEX Thermoplastic Sheet is a registered trademark of Kydex, LLC and is the only manufacturer of this material."
It is not plastic laminate, but a different material entirely. Plastic laminate will not form bullnose edges around a radius corner. It can form a bullnose edge on a very gentle curve though. This takes special forms, lots of time, money, etc.
From contributor G:
Kydex is actually a plastic laminate but not a laminated plastic. Over the years people have referred to high pressure laminate as "plastic" incorrectly. High pressure laminate (Formica, Wilsonart, etc.) is just paper laminated using high pressure and resin. Basically it's phenolic with a decorative top layer. This is why it will not stretch but only bend slightly. Kydex will stretch and form to any shape in a thermoforming process. Also, Kydex is a brand name which is why there is only one manufacturer. The same way Kleenex only has one manufacturer. There are other manufacturers of acrylic PVC. Dow being one that I know of but I'm sure there are a handful of others.
One of the biggest uses I'm aware of for Kydex is on hospital walls as it's one of the only materials certified for wall covering. It takes getting beat up pretty well, it's easy to clean, fairly chemical resistant, holds its color and looks good.
From the original questioner:
I really appreciate all the feedback. You have not only backed up my own experience via third party unassociated discussion, but answered my questions fantastically. Thanks for all your help!
The comments below were added after this Forum discussion was archived as a Knowledge Base article (add your comment).
Comment from contributor C:
This type of material is special powder coating for MDF. This material is very expensive to implement and it takes about a year to set it up.