Optimizing Fans in a Solar Kiln
Advice on housings and shrouds for kiln fans. December 31, 2013
Question
WOODWEB Member:
We have a solar kiln and need to make some changes to the fan's mounting panel. Would it help if the fans were mounted at the angle of the roof? This way the air would blow down the angle of the roof instead of at it straight on and give more air flow through the stack?
Forum Responses
(Sawing and Drying Forum)
From Professor Gene Wengert, forum technical advisor:
I doubt that this angled fan arrangement would change anything.
From contributor E:
Mine are mounted at a 30 degree angle (the roof is 45 degrees). Think it helps in two ways - first better air flow due to less resistance, second air does not lose as much heat because it is not hitting the cooler glass... It will not make a large difference, but every little bit helps.
From Professor Gene Wengert, forum technical advisor:
Perhaps more important than angle is to avoid any leaks, both in the upper chamber and around the lumber pile. If the fans do not have a housing that came with them, the housing you make should fit the fan's blade with minimal gap at the tips. For larger kilns, having the shroud curved like the Venturi of a carburetor will also increase efficiency. Avoid getting the fans too close to the rear wall, as this back space is also important, so get as much as possible. At the same time, do not move the fans too far forward as then you will have a dead space at the peak that will be hot. Avoid plastic parts that will melt when the kiln is not running.
I saw another post that indicated a solar kiln will get to 160 F. This would be without the air doing any work or evaporation. If a kiln gets this hot with lumber that is not fully dried, energy is being wasted rather than drying the wood... Maybe the fans are off.
I also saw a post that indicated that by changing the absorber's position in the dryer, efficiency would increase. The truth is that the size of the collector roof (perpendicular to the sun) determines how much energy goes into the dryer. If everything is painted black inside, you will absorb 100% of the incoming, which is perfect.
From the original questioner:
Thanks. The first thing we need to do is fix the fans, as they need a shroud because they are house fans, all metal. Then we need to close off the space above the fan board to the roof, as this is open and I think we lose air flow. We are looking for some plastic roof panels, as we have plastic covering the collector. The kiln has worked okay, just seems to take longer to dry then it should. Thanks for the help!
From Professor Gene Wengert, forum technical advisor:
Slow drying at the end? If so, the fans are coming on too soon and/or are running too late.
Are the vents mostly closed so that you develop heat?
Is the collector cover made of two layers spaced a little bit apart (even 4" apart is okay)?
Are the walls and floor insulated?
Fans size is important above 30% MC. More air is faster drying, to a point.
From the original questioner:
The walls and floor are insulated with 3" foam. We air dry to 30% before putting in the kiln. Close the vents all the way to start and turn the fans on at 9:00 am and off at 8:00 pm. We have a single layer of plastic. How far should the bottom layer be off the floor? We are using 1" thick stickers on the floor to start. Not sure of the fan size but need to have a shroud made for them.
From Professor Gene Wengert, forum technical advisor:
Two layers are much better.
A sticker on a flat floor should be okay.
Fan size is not too critical for under 25% MC, but heat is important. Are the vents closed mostly so the heat builds up?
From contributor B:
I built my solar kiln in 2002 and used 8mm double wall polycarb 4'x10' sheets (5 covered my 8' x 20' box with a 30° roof). I have been very happy with it. I also used common attic fans complete with their shrouds - I took the hoods off - and wired them into a thermostat that turns the fans on and off at preset temps (20° hotter than normal morning lows).
From contributor C:
I found raising the stock off the floor 5" really helped the bottom layer, which was a trouble area before. I made tees with 2x4s and used them for the bottom stickers.
From contributor B:
Depending on the size of the load I'm drying, I use either three or four 2' X 4' plywood panels painted black with a circular cutout for a fan. The fan is just a box fan, but I removed the metal standard that holds the motor and fan and mounted it on the plywood. The plywood has a 1" X 2" frame for rigidity. Once I get my stack in place, I just put the panels on top of the stack and lean them against the rear wall. It seems to work very well.
The collector is two layers of UV resistant greenhouse plastic spaced 6" apart. The kiln is well-insulated with foam insulation board. I get three loads per season, no problem.
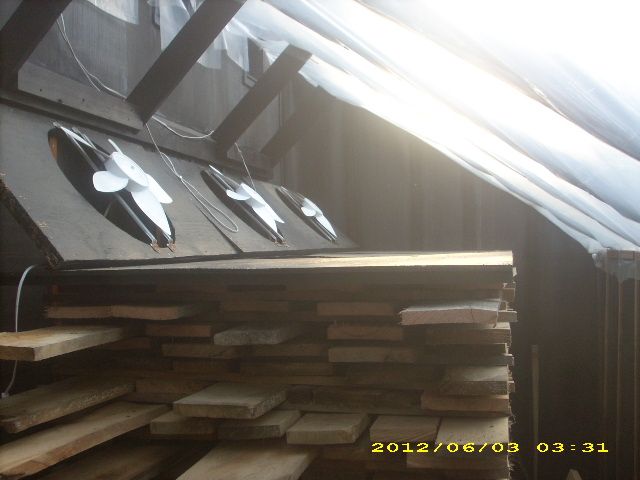
Click here for higher quality, full size image

Click here for higher quality, full size image
From Professor Gene Wengert, forum technical advisor:
Good looking. The fans will deliver more air if the blade tips are in line with the plywood and just enough clearance so they do not hit the plywood.
From contributor B:
I had actually considered making a circular shroud around the blade tips but never did. I keep the fans on low as it is, so if I want more circulation I can always turn them up to medium. Here's a table made from red oak and walnut lumber from my kiln.
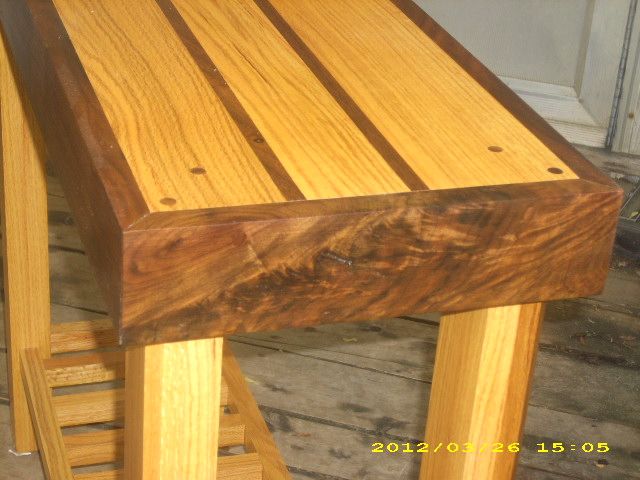
Click here for higher quality, full size image