New Shop Dust Collection
Other Versions
Spanish
A shop owner re-thinks everything from the ground up as he ponders the dust-collection system for his planned new shop. June 15, 2014
Question
I am going to be breaking ground for my 60x40 shop in the spring . I want to put my dust collection pipes in the floor before concrete. I am wondering what size pipe and type of pipe would be good for a concrete slab? I will be running the smaller shop tools - no moulder or CNC. The largest equipment would be a 24" planner, 37" wide belt and 8" jointer. I remember having under slab piping in our high school wood shop but that was seven years ago and I don't quite recall what they used. I have been playing around with placement for equipment for six months now. I pretty much have them down where they will stay. Any tips would be great.
Forum Responses
(Dust Collection and Safety Equipment Forum)
From contributor W:
I have a Clear-Vue cyclones hanging on the back wall waiting for the money to run all 6" irrigation pipe (overhead; the floor came with the shop, a 55x116' Q-barn).
From contributor S:
The idea of ducts in a concrete floor has always scared me big time. A year or two later when you get a different machine or move an existing one are you going to start cutting up the floor? Maybe even scarier, what happens if a duct gets plugged or a critter gets in one and dies?
From the original questioner:
I was trying to keep anything off the floor and have clear overhead room. I have seen most dust collectors have an 8" or 10" inlet. I guess I could run that as far as I can till I y off of the main at 6". As for dust collectors I am looking for a 5hp cyclone or something close. Any recommendations on any particular brand or cost? All we have at my full time job is two Powermatic two-baggers and two Grizzly one-baggers. That doesn't seem to cut if for me as there is dust all over.
From contributor U:
If you will always be working alone, then 6" runs everywhere seems fine. But if there is the future possibility of multiple people running different machines, then progressive sizing of main line and branches will allow for better and more balanced flow. There is a lot of wiggle room in duct sizing for a shop this size, so don't sweat it too much. Coming off the cyclone with the appropriate duct size, then branching down to two or more zones where machines might be used at the same time will help prevent future regrets. I run a 15 HP cyclone for a four man shop and we even upped the main line from 12" at the cyclone to 14" for a main trunk, and it stays clean inside. Opening all of the gates from furthest to closest to the collector once in a while is good insurance against chip buildup.
From Contributor K:
If you were doing this above ground you would be ok because as you discover inefficiencies you could make changes. There's more to it than providing a big enough branch to the individual tool, there's balancing the mains as well based on static pressure and overall CFM requirements. Remember, you start with determining the tool/tools CFM requirements, size the branches and the mains, determine the SP in the system then you'll know the blower size (CFM at a given SP) required to run the whole shop.
From contributor U:
It is definitely good to be aware of the basics of duct sizing. Remember that it doesn't make much difference if you just have one gate open at a time. My bias has been to get a blower with good low-pressure capabilities to help overcome static pressure losses.
From Contributor O:
Being a contrarian, I will recommend conventional pipe in the air, not buried. Any professional shop will undergo changes over time and with your ductwork literally set in stone you will not be able to change in an efficient manner. Shops have a tendency to grow, and a fixed duct system will not grow. I feel you are placing too high a value on keeping the ducts out of sight, while ignoring the real fact that everything changes. The last thing you want is to be confined to some antiquated process because you don't want to see dust pipe anywhere.
From Contributor E:
I have to agree with Contributor O, especially the duct work that goes to the table saw. I have to pull the flex hose off going to the duct work on a somewhat regular basis to pull the small off cuts that drop down into the saw then plug the hose up. I don't know what I would do if the duct work was in the floor. A zero clearance table insert isn't an option on a slider. That, along with the reasons Contributor O listed should be reason enough to never bury duct work under the floor.
From the original questioner:
Thanks for all the input. I will definitely be putting it up in the ceiling. Does anyone have any recommendations on any particular brand, cost and what model is most efficient? I’m looking at a 5 HP Cyclone from Laguna with 3600 cfm at 16" SP.
From contributor U:
Good call on ceiling mounting the ducting. I just completed my annual shop re-arranging to chase down a little more efficiency. I bought a shop full of used Nordfab ductwork years ago, and am still using up the last bits of it. It makes this ritual much easier.
The Laguna (or any 5 HP blower) is not 3600 cfm at 16" SP. Those numbers are just the max. So it would be 3600 CFM with clean filters and minimal ductwork (minimal SP), close off that ductwork and the absolute max static pressure that It could pull under those same conditions is 16". Try to get a fan curve out of them to see if this meets your needs after running a back of the napkin calculation of what the SP losses and CFM requirements will likely be in your shop. I think that a 5 HP cyclone is a pretty standard starting point for a one-man shop.
From contributor W:
I note from their website that the new owners of Clear-Vue Cyclones now offer a "max" unit with an 8" entry. That equates to 64 circular inches. Can be broken into two 6" ducts (2x36=72 circ in.) which would give two machines running concurrently with little appreciable loss (quick and dirty math), worth a second look. Especially if one of the tools attached has only two 4" dust ports. I'm laying my system out (one 6" inlet on my Clear-Vue) by using nothing greater than a 45* bend, 6" to each tool and 36 circ in of opening at each. Quick spreadsheet lets me calculate what size piping maintains the total.
From Contributor N:
I have a similar size shop and use a 5HP Oneida pro2000 and love it. I looked at the Clear-Vue quite a bit too, and ended up going with the Oneida but I don't remember why now. I think either one would be great.
From Contributor O:
I have used Oneida equipment and their layout service in three shops and see no reason to ever change. Send them a scale floor plan and CFM requirements of each piece. They will engineer the whole thing, their equipment is the best, and the whole system works well and is near bullet-proof. They are great people to deal with on all levels - very professional. The only thing I see as weak (and Oneida is not the only company guilty of this) is showing the dust going into a 30 or 44 gallon drum. A real shop will fill that in 20 minutes and then you have to empty it! I built a room of 128 cu/ft to contain the shavings, and empty it every week or two.
From Contributor E:
Another thing to consider about Clear-Vue is that all their brackets and motor mounts are built using MDF. I've heard of these things breaking due to the loads put on the MDF. Pay the extra money and go with Oneida.
From Contributor C:
"I've heard of these things breaking due to the loads put on the MDF." I find that very hard to believe. I own the CV max from Clear-Vue. My final decision fell between the CVMax and the Onieda. Knowing that both would do the job, I decided to call each company and talk to them about their product. I won’t go into detail but Clear-Vue had all the answers to my questions.
Three reasons I went with Clear-Vue:
1. 100% USA and paid Bill Pents a royalty for his design.
2. The cyclone is clear. You can see if you have an air leak in your dust bin by how the dust swirls in the cyclone.
3. Customer support. I had a list of questions I had written down to ask both companies. Clear-Vue was far more professional and had all the answers. I'm not saying one is better than the other, I'm just telling you a few things that led me choice.
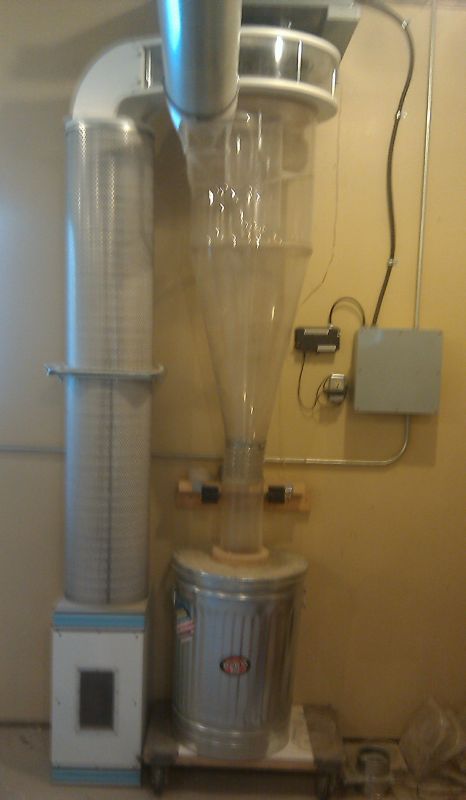
Click here for higher quality, full size image
From contributor A:
Floor ducting is fantastic when run in a crawl space or along the ceiling below the shop. You may need to address fire stop issues at the floor penetrations. As others have pointed out, putting it in a slab comes with issues.
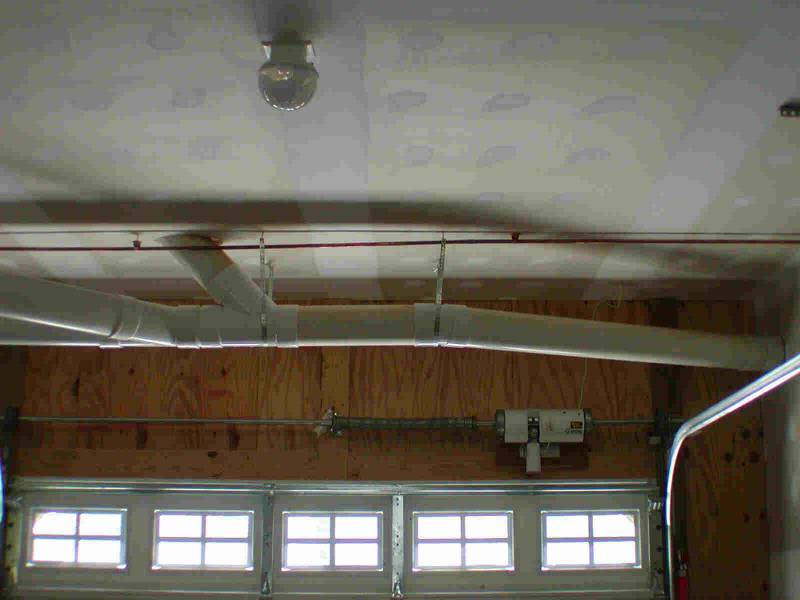
Click here for higher quality, full size image
"Photo by Alan Schaffter"
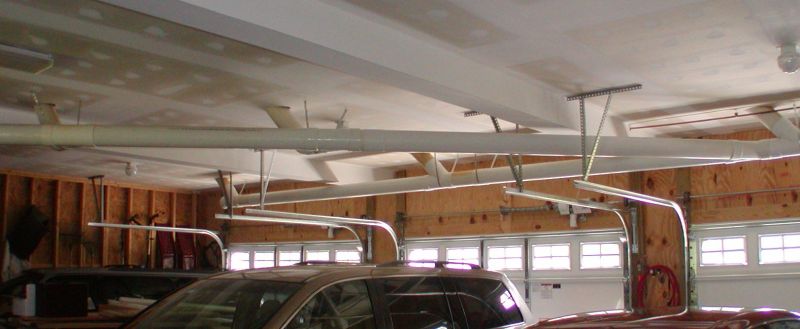
Click here for higher quality, full size image
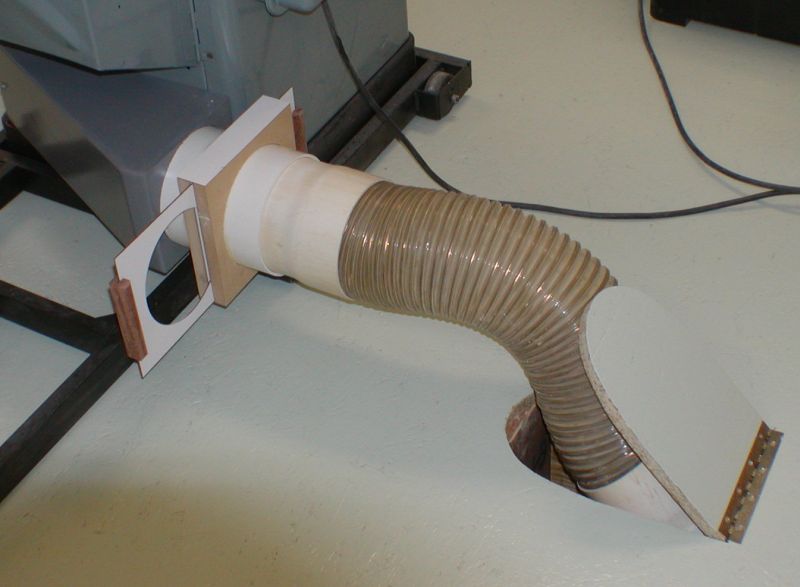
Click here for higher quality, full size image
From contributor G:
I avoided some of the disadvantages of in-slab dust collection by making forms and pouring the slab around them, thus creating channels with removable tops (steel in areas that take a lot of cart travel, plywood in others) like they do in factory settings. It takes some planning and a bit of extra expense, but works wonderfully well – it allows a certain amount of re-routing and good access for any major changes in duct size or such. I use them to route power, compressed air, and dust collection. They are about 12" x 12" - I can send you a drawing of the forms I built to pour them and how I strategized them to accommodate machine layout. I think those knocking the idea haven't considered making it accessible. I'm extremely happy I decided to do it that way and would encourage you to re-think the standard overhead model.
From contributor J:
For what it's worth, my one man shop has worked well for 17 years with a 3hp system from Oneida. With a 7" main duct, I leave a 4" port open at the table saw base for convenience and open up other ports as needed. I run one machine at a time, but the system can handle two at slightly diminished suction. If you plan to employ, consider a more powerful fan to handle multiple open gates. My system uses needled felt tube filters. I would be a little bit leery of the popular cartridge filters clogging with the fine dust from your wide belt. Perhaps someone with direct experience can advise on that.
From Contributor V:
I have in floor ducting in my 30x40' 1 man shop. The OP asked about size of duct, this is directly related to the flow capability of the cyclone. A typical 5hp cyclone like the Clear-Vue needs 6", running too big decreases the air velocity to the point where it may not carry the fine dust or even the larger chips any longer so beware. If this is a one man shop with a typical 5hp, 1200'ish real CFM then 6" will be fine. I really like ducting in-floor contrary to many opinions. Overhead pipe can be in the road but it also blocks significant light (unless you hang your lights below the pipe which compounds the clearance issues).
One issue to be concerned with for the under floor pipe in a concrete slab is water. You really don't want your DC pipe sitting in ground water as there will always be a chance it could leak, even if glued - not good. Make sure there is no change of ground water and you should be fine. In my case I wanted a framed wood joist floor rather than walking on a concrete slab all day so I purposely poured footings for the joists and left about 12" valleys below the footing level for my DC runs. I could then run pipe perpendicular to and below the joists, coming up through the floor when required. The framed floor also makes it possible to move the piping if needed as I can just pull up a few sheets of plywood.
If I were to do a concrete slab and place the ducts in the floor again I would place runs down all the walls to service all walls of the shop. You can come up out of the floor at one point and run horizontal above grade for the machines or estimate machine locations and put multiple ports near those locations to limit the above grade piping. I had a really good idea that my TS and other machines would be in a certain area in the middle of my floor and likely not move so I ran DC lines to that general area under floor too. The bottom line is if you ever have a situation where you need a line and it's not there you can always run above grade for that point. It still saves a lot of spaghetti overhead. All this said, I do realize it's not for everyone. If I had tons of headroom I probably would have gone overhead and suspended my lighting. Same for big shops with numerous employees, a big DC needs big pipe which isn't practical under a slab.
From contributor G:
I built a 42x80 shop eight years ago and put most of the ductwork in the floor. I had the system (7 1/2 HP cyclone) designed by a local company to make sure it was correctly done. There is overhead ductwork along the walls which allows for movement of those machines, but the center of the shop is wide open. I wouldn't have it any other way. I had my shop well thought out as to machine placement and probable expansion areas and have not regretted the decision one bit. Plan ahead and everything will be fine.
I used galvanized spiral duct everywhere and wrapped it with self-adhesive rubberized tape (6" wide like is used around windows for weatherproofing) to add a second layer of protection against rust in the underground areas. I love my system and really like having no obstructions in the main working area. Go for it, you'll love it. The naysayers have probably never had a system like this and therefore have no idea what they are missing.
From Contributor T:
As has been noted several times already the folks at Oneida Air Systems are a tremendous resource from engineering to delivering the (in my opinion) best American made equipment. I have an Oneida 5hp Pro unit and they designed the ducting and all machine pickups. Best money I've ever spent on dust collection!
From contributor D:
We used Oneida in 2008 when I built our shop and are very happy. Don't forget electrical conduit!
From Contributor I:
For the sake of accuracy about the discussions surrounding PVC pipe for DC, NFPA (National Fire Protective Association) rules prohibit PVC piping for dust collection in commercial shops. More than likely your local fire dept. is a member of NFPA. But not every fire dept. actually understands DC. My experience here in a major metropolitan area was that the FD wanted to know if my system was adequately grounded. I offered to show them that every piece of machinery was absolutely grounded from machine to the collector itself, and that was the end of that discussion.
From Contributor M:
I agree with everyone on the overhead ducting as well as staying away from PVC. It’s illegal for commercial shops I believe for spark/fire issues. The only reason I am commenting is that the one thing you really need to be careful of is making sure you have enough CFM. How far tools are away from the DC, how many bends and the degrees of bends all add up and in the end you could have not enough air down the line. You could go out and hire a consultant, but a lot of the time bigger DC companies can give you a pretty accurate idea of the CFM needed. Also remember that your after filters play a big role in maintaining that CFM. They clog up and the CFM goes down. Find out what filter media would be best for your shop - do you need to pick up a lot of fines, coarse or both? Then go from there.
From Contributor M:
I forgot to mention that spiral pipe is fairly inexpensive and works great for ducting. You can have it made to any size you like.
From contributor B:
I would stay away from PVC or any type of plastic. If you look up the drag coefficient of PVC vs. steel (spiral or smooth) there is a major difference.