Making Square and Octagonal Handrail Caps
Is a CNC router or an old-school rotary lathe the best way to machine a profiled square cap for a newel post? February 27, 2015
Question (WOODWEB Member) :
I'm looking to make square newel caps that match the 6210 handrail 6"x6". Can someone send me to the right place for shaper knives? I'm a turning guy - not a whole lot of experience here.
Forum Responses
(Architectural Woodworking Forum)
From Contributor O:
The trick is holding the part while shaping.
From the original questioner:
I figured I'd make a fixture to hold it but it is definitely a little scary for me.
From contributor L:
Make the fixture massive, fasten the work securely.
From Contributor O:
Being a turning guy, you may be aware of the old Matison 69 lathes that can do octagonal and other faceted work. This is what others used to use for shapes like you propose. The huge rotating cutters are genuinely terrifying, but they can make a newel in about nine seconds, and are the only things that can do the faceted work outside of CNC lathes.
From the original questioner:
I'm familiar with rotary lathes though I've never seen one up close. I don't understand though how you would get faceted newel from one. Does the cutter head (or the turning blank) move on another axis? The cap I am looking at making is 6 inches square. Would a rotary lathe have that kind of capacity?
From Contributor O:
Some of those lathes have a modification that puts the work holding spindles/centers on a cam so that as the piece rotates - usually just over a full rotation - it is fed into and out of the rotating cutterhead. The cam can be 4, 6, 8 sided. This cam can also be designed to provide rounded corners or sharp edges. I would think the way to do it today is CNC. Those lathe heads cost a fortune to build up and many parts must be run to pay for just the set-up. But they are very cool in an industrial way.
From the original questioner:
Interesting. I don't know of another way to do what you are describing. A CNC router couldn't do it, at least not efficiently (would have to carve four sides). Maybe a long hauncher would work? I've heard of rotary heads costing as much as $150 an inch. It would be fast and efficient for mass production but not very good for the custom market.
From contributor L:
A CNC router can happily carve 4 sides! What am I missing?
From the original questioner:
I guess all I'm saying is that a machine that can do it in nine seconds is pretty efficient.
From contributor L:
Doing it in nine seconds isn't efficient if you just need one! A router may take ten minutes to carve it and 20 minutes to program and have a change over time of two minutes, at most? Our 4 axis machine can do a lot - top, sides, ends without repositioning. A 5 axis that can put the work into rotation, lots more!
From Contributor b:
Traditional square or octagon handrail caps were referred to as "miter-caps" because they were assembled from mitered pieces (not milled). This is still the correct way of making these. Take 6210 rail, rip off one edge (or leave half the width of the rail). Cut and miter four pieces together. If you need a larger square cap you'll end up with a square opening in the middle. Cover this with a square rosette or mitered molding detail. Adjoining handrails are made by cutting the straight handrail to a point to intersect mitered pieces of the cap. The whole operation is done on the bench and faster than I can write about it (no tooling required). I've milled them too but this is definitely not as good due to the end-grain on two sides.
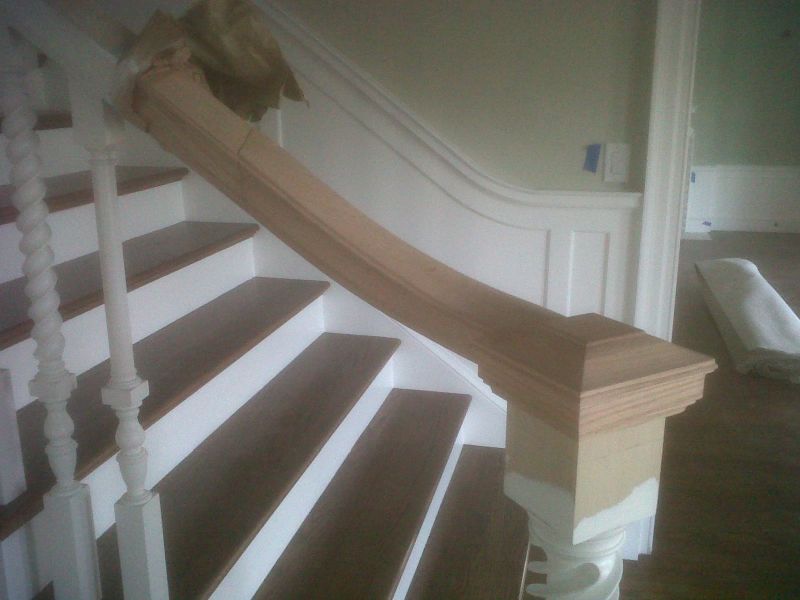
Click here for higher quality, full size image
From the original questioner:
This is probably what I should do and may wind up doing. The originals were one piece mahogany, and although they weren't exactly a 6210 rail the customer said she could live with it
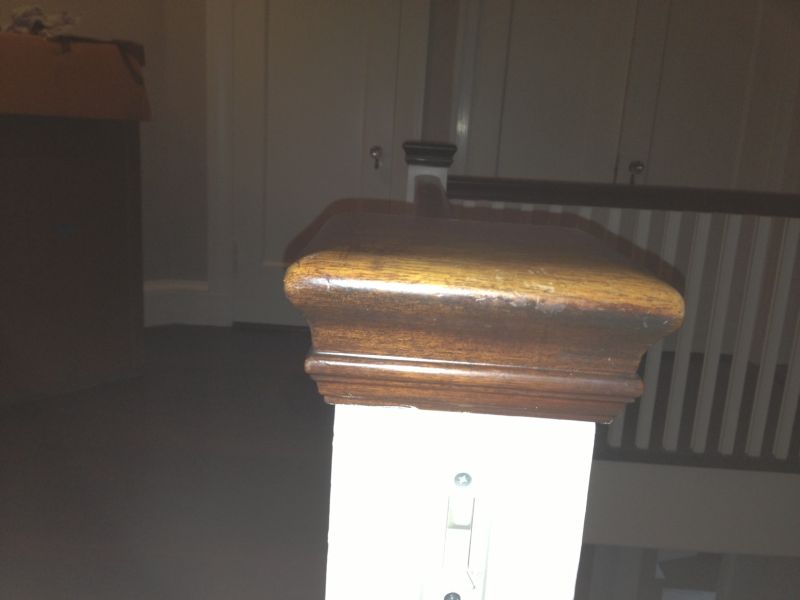
Click here for higher quality, full size image
From Contributor b:
Well that's a very nice handrail and certainly nicer than 6210. I would make this on a pin router and the required tooling would be one custom router bit (no programming required). Your customer shouldn't be asked to live with something less if she's willing to pay a little more. Matison lathes are truly magnificent and nothing really compares with them. Operating expenses can be huge though. Besides the enormous cost of building heads, a production line of Matison lathes requires big cyclone dust collection with a monthly utility bill exceeding 30 g's (at least that's what the factory foreman told me). Even with that, the dust was everywhere and all over the surrounding cars and community. The factory finally closed after more than fifty years. Typical square turnings like these are no problem for an old Matison (and hard maple to boot)!
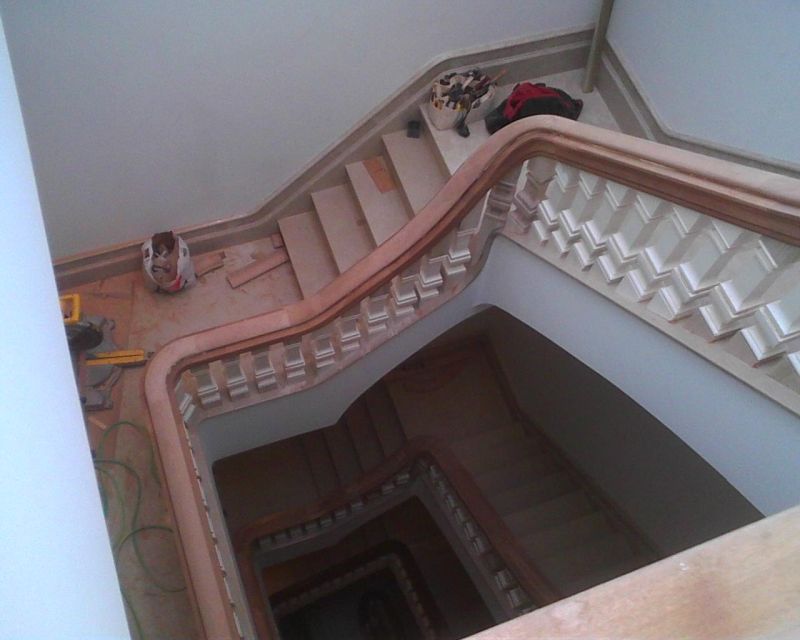
Click here for higher quality, full size image
From Contributor O:
The stair shop I worked in back in the 70's bought all their newels and spindles from Indiana Handle in Paoli, IN. Indiana Handle got their start during the Civil War making ax handles. They had a line of several Matison rotating lathe head machines, all hopper fed, and could make 4x4 red oak newels in nine seconds, then on to a similar machine that sanded them. I heard we paid $1.00 each for turning, $.50 for the sanding, but bought a couple hundred at a time. The company I worked for actually 'owned' the lathe heads, and they were not used for any other customer of the Handle Co. Indiana Handle also made every croquet set sold in N America - from the green wood to assembly, to finish, to packaged product, boxed and ready for sale.