Making Arched Raised-Panel Valances
Old pros advise a beginner on accomplishing an ambitious detail. June 5, 2006
Question
Seeing some of the amazing work done by some of the pros on this website got me inspired for my next kitchen project and now I'm wondering how I would go about building an arched raised panel valance. Do you have to make your own templates for the curved bottom rails and the two panels with a router-trammel setup, or do they sell prefab templates anywhere?
Forum Responses
(Cabinetmaking Forum)
From contributor J:
To answer that question to your satisfaction, I think most of us need to know what machines you would use to build it. I would begin by making a full size drawing of the valance on 1/8" masonite or some other inexpensive material. Anytime I have curved or irregular work, I make a drawing/template. From the drawing I would make a full size template and use a cutter with a bearing to cut identical pieces... This can be done with either a router and a flush trim pattern bit or a shaper and a rub collar/bearing.
From the original questioner:
I've got a 6"jointer, 13" planer, two table mounted routers, contractor's table saw, but no bandsaw yet. I've been making do with a Bosch jigsaw for arched door profiles and some door templates from Rockler.
From contributor Y:
Having built many arched (and curved) raised panel doors, wainscot panels, valances, etc., I can assure you that the pros on this website that run truly profitable and growing companies use the most important tool in their shop to produce these labor intensive parts. Their telephone.
Your post suggests that you may be the anomaly. The tools you have will work to produce what you want. Carefully think it through (and always think safety first) and your results will be satisfactory. Remember that preparation always takes longer than production. The problem is that the time (and expense) learning and perfecting how to build these parts is wasted. If you're in business, it's more important to know what not to build than it is how to build it.
Do you have a CAD program? This will be the best place to start. Much easier to make changes with a keystroke and a mouse than a pencil. You can get by without a bandsaw, but it can be helpful. There are many ways to accomplish the same thing. In woodworking, it is a matter of time and money. Specialized tools generally contribute accuracy and time, but you pay for that. Plan on using your routers on a circle-cutting jig for templates. A CAD program can help you find your radii and offsets. If your valance is going to set away from the wall, and the top will be curved, you will want to know more about bent wood laminations.
From contributor G:
Sounds like you already know how to build the valance. Yes, make your own templates, use trammel points and have fun. I just finished building one today. I can easily build one cheaper than ordering it. The advice about the time being wasted to learn this procedure is about the worst advice I have ever read on this forum. This could be a very worthwhile experience that you can use for the rest of your life. Just because one person doesn't have the ability to profit from such work does not mean you or I can't. You will not make money the first time you build one of these, but the experience will be worth it. Monday I will build another double panel arched valance. It will be 9 1/2" wider then today's and oak instead of cherry. I will draw it out full size first, make templates and go at it. I will make good money at it and have it in a fraction of the time it would take to outsource it. As a bonus, I will even be proud of it when it is finished.
From contributor G:
As I mentioned earlier, I make a full size drawing using trammel points to draw the arcs. I do this trial and error to find the correct radius. You could figure it with geometry. I slightly flatten a spot on the top of the arced bottom rail where the center stile meets it. This is easier then arcing the center rail tongue cut. It is not obvious to the eye. I make a pattern that follows a guide bearing to machine the groove cut in the top edge of the arced bottom rail. The pattern is fastened to an over-width bottom rail that at this stage is still straight on the bottom. All other cope and stick cuts are done conventionally since they are straight. I then dry assemble the unit, flip it upside down on the panel blanks and angle my pencil up to the bead profile to trace the panel shapes. This gives me the extra 5/16" (by the time I cut on the outside of the line) on the panel to go into the groove with Spaceballs. Three sides are straight, so they are easy. The arced edge must be cut and sanded smoothly to create a flowing fair curve. This edge follows a guide bearing under or above the panel raiser. Any error in this edge will transfer to the raised profile and show. You could make a template for this and save it for future use, but seems every one I make is an odd size, so I don't make a template. Assemble the valance and cut the bottom arc with a bandsaw and sanding or a router and trammel. After you make one or two of them, the mystery is gone and they go fairly quickly.
From contributor K:
I use a shop made router circle cutting jig to cut all the arched pieces. It is adjustable by adding length to cut a 100 inch radius. It is very accurate and easy to use.
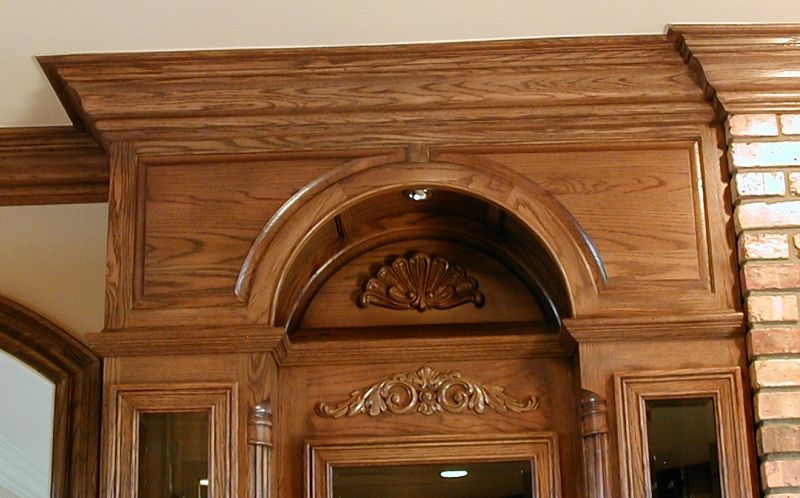
Click here for full size image
From contributor J:
I make arched raised panel valances on a regular basis, from 24"r - 202.375"r. Don't use any templates, though. I've got all my cabinet files in AutoCAD lt. My valance file is similar to a raised panel drawer front with lower rail having the arch. Size the drawing to the required size - this will give you the parts list and the radius of the lower rail. I take the radius, set up the shaper with the front pivot (I custom made the front pivot assembly), and set to the radius needed. Cope the rails first, do a rough cut on the band saw, then attach the lower rail to the radius attachment. Using the power feeder, climb cut the lower rail through the shaper with the sticking cutter on. Lower rail completed. As for the panel, mark out the radius needed, band saw to line, sand carefully. The better you do here, the better the end result. Then put the appropriate dead collar on with the panel raiser and shape the panel. The rest is the same as any other 5 piece drawer/door. You can do the same thing with mitered joints as well.
From the original questioner:
Thanks for the responses! Contributor K, that is some beautiful work - simultaneously inspiring and humbling.
From contributor F:
I have a long shop built router trammel. It's 20 feet long fully assembled. The purpose of these isn't necessarily to execute extremely large curves. These make it possible to accurately cut curves of a large radius that have less extreme curvature. A good tip for using a router trammel to cut curves is to set the final pass in depth to leave a "web" of material about 1/6" thick holding the part to the scrap. This way the part can be fastened to the bench with screws through the waste portion. The parts can then be quickly trimmed with a flush trim bit to clean off the web.