Hold-Down Problem when Profiling MDF Panels
MDF panels may bow or warp when large amounts of skin are removed from one face. Here's how to deal with the problem. June 5, 2006
Question
I received a commission to machine a large 2800 X 1800 X 25 thick piece of MDF to make a mould pattern. I placed the board on my CNC Vacuum table with about 1/2 on the table and 1/2 off the table, my table only machines 3250 X 1080 but is open ended so I wanted to machine half, turn it around and complete the machining.
It started off great and machined about 98% of the first side, moving from left to right. The dust hood was down and all looked fantastic. When it stopped to allow me to turn the board around I noticed that in the last 2% the tool had looked like it had come loose and started to gouge to board, obviously wrecking the whole job.
I checked the tool holder and it was perfect, it was then that I looked and saw that the board had lost hold down and bent up to meet the tool, and thereby causing the tool to take a 5mm deeper cut than intended on that corner section. I cut the board in half to make it easier to throw away and then took the boards off the machine. I then noticed that the whole board had "warped and bowed" and I was just lucky to have got so far in the machining sequence.
So the question is - how do I stop this from happening in the future? Obviously the vacuum hold down is no good, but what do you do when faced with this problem?
Forum Responses
(CNC Forum)
From contributor B:
MDF and particle board have outer skin surfaces that have a higher density then the main core area of the sheet. This is more obvious when you look at the edges of a sheet of particle board but is the case with MDF as well. This denser area is perhaps 1/16" to 1/8" thick. This gives a harder surface to the material while keeping weight and cost lower then if the entire thickness were at that heavier density.
When you machined away the surface of one side you released the tension that is generated by the dense skin. That allowed the other side, which remained under tension, to bow the sheet upwards at the edges. To solve it you have to machine both sides of the board evenly. To hold it you'll have to add hold down blocks at the edges.
From contributor J:
I've had this happen, too, but not all the time, which leads me to think it might be a moisture issue. If the weather has changed recently the outside of the MDF might be wetter or drier than the inside and by machining away one outside you may have affected the balance of the panel.
If it is a density issue, you could try a type of MDF with a more even density all the way through. Here in the US we have a product called Rangerboard, which is made from more refined pulp and is the same density all the way through.
From contributor D:
We produce carved architectural panels out of MDF and other materials. Many of the patterns require machining of the entire panel face. Frequently these panels will have stress in them and will try to curl up at the edges. This results in anything from a little chatter at the corners to a completely ruined panel. Our "fix" is not very elegant. We tape all the way around the panel with masking tape so that the edges do not lift. Additionally we mask off any unused bed so that we keep the deepest possible vacuum. This method does not always allow us to release a badly warped panel and reposition it. Warpage can vary greatly from panel to panel and vendor to vendor, but as Contributor B observed, the faces of the panel always appear to be in compressive stress.
From contributor M:
Here are a couple thoughts to resolve the problem you have.
1.) You state that this will be some type of mould when you are done with it. Can you possibly apply it to a substrate to stiffen it before you machine it? Maybe you could try something like a 1" plywood base to hold flat and straight?
2.) See if your local supplier can get you a homogenous board. This type of board will not warp as much as the standard MDF because it has uniform density throughout the panel.
From the original questioner:
I was dreading having to skim both surfaces, only because I am a 1 man shop and a piece of board this size is really difficult to move around, but I think I must do that. I did measure the MC content and it is 10.5 so I contacted the vendor and asked them what it should be, they responded that around 12% would be about ok. Personally I thought it should be about 4% as the sheets are "cooked" when manufactured.
Contributor D - after you machine panels like this do they go back to being flat once removed from the machine or do they have to be mechanically flattened?
From contributor D:
Generally speaking, the panels never lay perfectly flat after machining. It would be great if they did, but we have to point out in our installation guide that some warp is unavoidable.
From contributor B:
If you machine the dense surface off both sides the panel should lie flat once removed from the cnc.
From contributor M:
To the original questioner: This is going to be a vacuum mould for plastics. Unless there are some size restrictions for the thickness starting with a thicker piece should not be a problem. They will simply pull the vacuum through a little more material. Can you clarify if this is going to be concave or convex (male/female) mould?
From the original questioner:
You are right on the money it is an acrylic mould and will have a convex face. What I did yesterday is plane both sides by 0.2mm and then I stuck it to the table with double stick tape and then I also use small gang nail plates to nail the 25mm board to my standard spoil board.
The first pass was perfect, and then I had a proximity sensor go down on the tool change on my CNC so we have fixed that and hope to finish machining soon. As for thicker material, I am only a small guy and this one is heavy enough already.
From contributor S:
Is the issue here that possibly as you cut away material, the vacuum is just sucking air through the material? If you are using an upcut bit, is it drawing the material up off of the table due to the lack of vacuum? I cut only MDF and yes it has warped but not usually that quickly. It will warp if we let it sit without dealing with it soon enough.
From the original questioner:
Here is the finished product below. Yes I was using an upcut 2 flute, but because of the machine design that is sucking up the trash through the hood, I think this too helps to release vacuum. Next time I will use a 0 single flute and no up or down tools, but I also think I got a poor piece of MDF to start with, as it has now bowed to about 65mm in the centre.
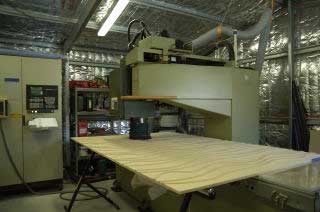