Fence Adjustment Issues with Cope and Stick Cutting
A discussion of jigs and methods that make cope-and-stick setup efficient and simple. September 27, 2009
Question
I’m about to throw most of my cope and stick cutters at the ground, all of two, one being a Freud multi-profile set. Why would these standard profiles be designed where it would be necessary for the operator to set up his fence twice for stacked cutters? I’m assuming that neither cut should effect the overall width in the case of the stick, nor the overall length in the case of the cope. Can anyone shed some light on my frustration?
Forum Responses
(Cabinetmaking Forum)
From contributor K:
Buy multiple shapers and leave each one set up for only one task. It really speeds things up.
From the original questioner:
I actually have three shapers but only like one of them. I am not by any means a production shop, I just want things to be easier like a production shop. I would just like some real understanding from experienced cabinet door makers of what the cutter manufactures had intended. I have a set of grizzly cutters that are spindle height adjustment only, no fence adjustment needed, nor do they take off more material than necessary.
From contributor M:
How about Freeborn?
From the original questioner:
I have an older set of stacked freeborn cutters, same thing, the fence has to be adjusted to fit the cope and stick perfectly.
From contributor L:
I have cutters made by LRH and they also remove stock. I like it this way. It gives you the perfect mate. I set my stick cut to remove 1/16". This means I can have a cut edge and a jointed edge. I put the cut edge against the fence of the stick cut and it removes a bit of stock and now I have a smooth cut, no saw marks and I don't need the extra step of milling to make both sides jointed. I remove 1/64" from each side of my cope. This again gives the perfect mate and allows the cope action to make the cut perfectly square in case it wasn't to begin with.
From contributor S:
I guess I don't understand why you would want to remove stock to get a perfect fit. I use several brands - Amana, CMT, Sommerfeld - all have rub collars. I use separate bits for all cuts - no multi-cut bits. But I never have any trouble getting a perfect fit.
From contributor A:
You can purchase rub collars for most sets. They are used when doing curved rails. I don't understand why you are setting up your fence twice. Ideally like contributor L mentioned you do want to remove a bit of material. If you do your copes with a miter gauge or sliding table fixture there is no fence required. The fence is only required for the pattern cut, which should be the second cut.
The KISS method you are imagining is to do your cope cuts with the fence moved back out of the way. Then throw on your pattern cutters with the rub collar. Using a steel ruler move the fence so that the bearing is proud of the fence by a bit. Now the power feed will force the profiled parts into the cutter head. This should be possible with no test cuts as long as the cutter heads are at the same height.
From contributor K:
If I had to do it on a single machine and the cutters needed a different fence setting I would make a shim for the fence the thickness needed for the task. That way instead of time consuming small adjustments, just drop the shim in place and go.
From contributor A:
Every shop I have ever been close enough to see how they do it, as well as my shop, all do it the same way.
Cabinet doors, passage doors, etc: Stack cope and stick cutters on the same spindle. Set the cope fences where they need to be and set the height. Then make and place another fence that will run back to back with the first fence, and build up the table to mate to the sticking cutters (or vice-versa). Use the 'other' side of the spindle, so to speak. Then there is no adjusting, no magic or cuss words, just cutting wood. Feeders still work, etc. Run the dust port out of the top of the fences and a second port below the table.
If you need more than one pattern, load copes on one machine, and sticks on the other, all with offset tables and fences. Yes, the problem is then curves, but have a couple of router bits made for them or another set of cutters. This will also work in other operations once you see how simple it is.
From contributor L:
Funny, every shop I have worked in has had the cutters on different shapers. No setup time just walk over and push on, you're ready to make parts. That is how I have mine setup.
From contributor V:
The real reason to remove width from your stock on a sticking cut and length from a rail on a cope cut is that it is the only way to be sure you are getting the entire profile cut into your material. Wood is always slightly imperfect and to try to just "nail it" and remove nothing would leave areas undercut. I use a fence on a cope cut, how else can you register that cut from a sled or jig?
From contributor L:
I too use a full length fence for my cope cuts, it is offset by 1/64" from the infeed to out feed. A few shops I use to work for just used a block of wood clamped down and then the sled had either spin-tite or pneumatic hold downs to keep the pc registered at the proper distance from the cutter. I like my way better. No need to clamp the pc down, makes it faster to flip pieces around and put a new one in. It has its advantages on wide pieces though.
From contributor V:
Sounds like a good way contributor L. The way I get around fence adjustments is by using a shop made fence system. I have a main fence structure that supports sub fences and has the dust collection port. I screw the working (sub) fences to that main structure. By using different thicknesses of sub fences I eliminate the need to measure and move the main fence between between cope and stick or what have you. I do the same thing with the elevation of the cuts with "sub tables" of varying thicknesses. To have three shapers would be nice too!
From contributor L:
Sure is nice to have them setup all the time. Just walk over and press on and start feeding wood.
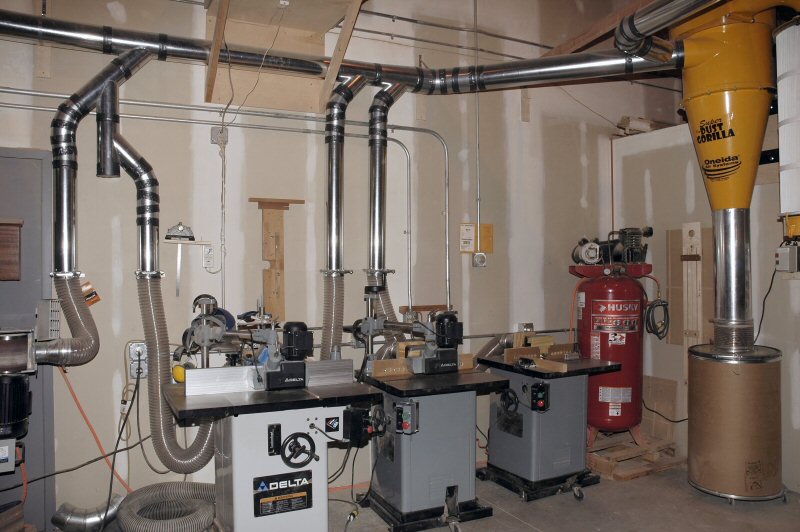
Click here for higher quality, full size image
"Photo by Leo G.".
From the original questioner:
You all have great ideas but I would like to hear from the guys that are using industrial shapers, such as a Martin, Scmi,etc. Not that the size of the machine matters so much, but these shapers were not designed with the intention of setting up being so complex, aux fences, elaborate jigs and such. I have a Scmi T130 with inboard adjusting fence only that can adjust to less than 1/64 of an inch. I have heard of rub collars being used on curved cuts with a template that rides the rub collar not the material. My experience is that rub collars are not intended to touch the actual material being milled because it burns the heck out of it. If I can dial in my fence in just to make the cut that is necessary then I see no reason to compensate with extra material, more software adjustments, more shop thinking, and more fence fiddling.
Here is what I would like - stack the cutters, it doesn’t matter which is on top or bottom, adjust and square the fence with the sled for the cope cut so you butt the cope end to the fence as a guide. Then make all cope cuts, remove the sled, swing the feeder in to place and finally run the stick cuts. Also I clean edge all material on my shaper with helical head, door parts, face frame material etc.
From contributor L:
A rub collar is a bearing. It has to touch the wood. It shouldn't burn the wood unless the bearing is bad.
From contributor O:
The Freud multi profile set is a difficult setup. A contractor paid for ours to match existing
cabinet doors he had on a job. It is the RS 1000. I don’t think the other posters understand how this cutter works. You do have to set the fence and spindle twice. I have a Martin programmable shaper and would say this is the most difficult cope and stick I have ever experienced. To get repeatable results you would need to keep material thickness consistent from job to job and devise some method to set the fence and spindle if not programmable. We have a Garniga cabinet set that works on a similar principal but it is easy to set. I built four
cabinet doors with this and hope to never use it again.
From the original questioner:
Thanks for making me not feel crazy here. How much did you pay for your Garniga set? As I said though my freeborn set is the same situation even though they are not insert interlocking style cutters, fence in and out for the cope then stick to match. Does anyone have a picture of the cutters used with a rub collar, is it 1/4 tall? Is it only used for stick cut? Does it ride on the bottom of "rabbet" portion of the cut?
From contributor U:
Can you just make a fence with a shallow rebate (or step if you want to think of it this way) that would let the sticking register where it needed to on the table, and the rails where they need to at sled height?
From contributor O:
The Garniga set was about $1500 including the panel raiser a few years ago. Freud’s industrial line is good but that multi profile set is hobby grade. It did not cost that much. The Garniga set only requires a height change, no fence movement. If I were doing a lot of
cabinet doors I would buy an additional cutter so you could have two shapers set or stack both cope and stick. The advantage of these multi profile sets is they do a lot of different stile edges and the glass door cuts. The disadvantage is a little more setup for the different cuts.
From contributor A:
So let me get this right. You are doing your shaper door copes similar to using a miter gauge on a tablesaw? On the tablesaws you would clamp a scrap piece to the fence. That would determine the location of the cut. It would give enough offset so that the fence would not bind the part. You simply hold the part down with your hand and push the miter gauge. That procedure would be common for doing shiplaps with a dado set. It sounds like you are doing a similar procedure on the shaper for door parts. We have always used a sliding table shaper with a clamp fixture.
From contributor L:
I have a full fence with a 1/64" offset. I use a TS miter gauge to hold the part. I have an 18" board that almost touches the fence (attached to the miter gauge) and sand paper glued to the miter gauge board – it’s used to stabilize longer pieces and for a blowout block. I’ve been doing it this way forever and haven’t had any problems.
From contributor R:
It's called the common minor diameter of the cutters, I use 1 1/4'' bore Byrd cutters, stacked with cope on top and my sled is milled to the exact thickness so I don’t have to adjust the fence or spindle.
From the original questioner:
I noticed Freeborn advertise the same thing, minor diameter cutters. What does, or should the diameter have to do with the depth of the cope and stick cut? The larger diameter cutters are supposed to make a cleaner cut, how does that come into play? I realize now what my original confusion is. The fence does not need to be adjusted, if you set your cope cut first to make a full cut with the infeed fence set back to the exact difference of the two cuts with the outfeed fence out of the way. Then place outfeed fence back in place and run your stick, taking out, in my case 3/32 of material off the original width, making it a 15/32 long tongue and groove with 3/8 profile cut. I guess I just have to change my habits and compensate the extra material on my cut list. Thinking more about the rub collar I don't see how it’s possible to set up, considering the stick cut is the full thickness of your material. Where does the rub collar ride?
From contributor L:
The minor diameter should be the same making the fence distance equal. Usually the minor diameter is the cutter that takes that little bit of material off.
From contributor O:
You’re right about the fence remaining the same for this set. I dug out the cutter drawings and my notes from the one time use of this set. With the fence offset it is the same. From my notes my problem was in the shimming of the cutters. Freud’s conversion of a metric cutter head to inch dimensions adds to the confusion. With the design of this set it is not possible to use a rub collar unless with a pattern above or below the work piece. It is best to remove 1mm or whatever with both the cope and stick cut with this type cutter.