Fabricating Pyramid-Shaped Raised Panels
Advice and thoughts on how to machine a raised door panel that looks like a very low pitched hip roof. November 5, 2013
Question
(WOODWEB Member):
My customer presented me with a design which uses a raised panel that comes to a point. Think of a pyramid. The largest size panel would be 12" wide x 24" tall. It would be in a typical stile and rail construction. This is repeated, in various sizes, around the kitchen. The wood is quartered white oak, and it is stained to highlight the 1/4 cut. So it must be precise in its form, and sanded carefully. How can this be done? The designer talked about this being a common feature in Victorian era homes (pre-cnc) no doubt. Any thoughts on how to proceed?
Forum Responses
(Cabinetmaking Forum)
From contributor L:
I did about 30 of these about 3 years ago. They were getting gold leaf so the doors were cut from MDF. We cut them with a ball mill on the CNC a 3-D tool path. There were several sizes and some of the pyramids were very shallow. You could do the same in solid quarter sawn white oak. I would suggest cutting both sides. We prototyped one side only and they warped.
From contributor C:
Make a sled for the thickness planer set at your desired angle. Flat cut that fits into grooves of rails and stiles on a table saw. Sand transition from flat to angle of face. Old school, low tech but you need a pretty big planer.
From contributor R:
Dare I suggest you could use a sharp jack plane to raise the panels, especially the smaller ones? I would think that, depending on the number of panels, it would be quicker to plane them than to set up a machine, including a CNC, to cut them. Also, wouldn't the slight angle of the panel diminish the quarter-sawn figure in the white oak?
From contributor D:
Triangular panels are common in cross buck passage doors, and raised on both sides to boot! You do not mention the raise profile - hip, cove, ogee, step or whatever, but the procedure is the same. It does not require CNC, just good old woodworker problem solving.
This is most often done sequentially, with a sled. Do not profile the second side of the point trailing on the shaper, make it the first cut. Use a sled and a backup edge strip to support the point on both the first and second cuts. You can even use some 2-sided tape to hold it all together. Have some extra stock ready to go - broken tipped panels make excellent firewood.
From contributor L:
I am a fantastic woodworker that now uses the extreme precision and repeatability of a CNC. So this can be done both analog and digitally. Good luck with your project either way.
From contributor P:
Bear in mind that unless your panels are square, you have 2 different angles to cut to achieve a single point in the middle.
If you care to outsource your doors, Meridian offers 2 different variations on this panel style, one where there's a single point in the middle, and the other way has both angles the same, resulting in a ridge instead of a single point.
From the original questioner:
Thank you all for your comments. You helped me sort out some of the processes involved with this job. Although it is in the bidding stage at this point, it's nice to know what one is getting in for. I do have some good hand planes, but I think the precision of the CNC is really what I need.
From contributor D:
I mean no disrespect to the CNC people out there, but I have never been able to get pricing from anyone on such work. I have sought such work about 15 times over the years, before I gave up. The programming is always the hitch - no one has ever been able to tell me how much something will cost until after they do it - that doesn't work very well with me or my customers.
So… let me specify what we are talking about and let's see if anyone wants to offer a price - either publicly or privately.
Let's say 4 panels, all the same size - 14" to a side - and angles at 30 degrees each. To simplify the charges, I will supply 5 panels all sized and ready to go - with one to waste. The profile will be a double hip raise, conventional traditional style, at 1-3/4" wide, total of 1/2" deep in a 3/4" thick panel. I'll let you determine the angles you like. All work on only one side of the panel. I'll do the sanding, and for the sake of simplicity, I'll pay any transport fees for the panels, to and from.
I assume this will involve custom tooling, and that would be part of the price. Anyone care to bid the work?
From contributor L:
Typically I will run a test drawing and part of a program before I submit a bid. This is done at my expense. I gain two things - one, a fixed price for my customer and two, I know I have a method to program and machine before I say yes, I can do that. No disrespect taken. I was an all handmade guy for many years and still am with some things.
From contributor D:
Do you care to offer a price? I'm looking for someone - anyone - to prove me wrong. To prove to me or any other interested party that they can and will price out millwork for those of us that may be in need of their services.
This is probably the third time I have offered a simple similar challenge on WOODWEB to CNC vendors, and I have never yet gotten a complete number. Yet many threads suggest getting a CNC to do this or that. Something tells me that it is not really a viable solution.
The skeptical side of me has had encounters with snake oil/CNC salesmen that have encouraged me to buy CNC or just go out of business. My work and my particular way of enjoying my work does not include CNC type work. I prefer the skills and challenges of old school. However, I have needed 2,000 l/f of egg and dart, and some logos done in wood door panels and.... But could never get anyone to actually give me a number I could use.
From contributor C:
It seems to me that you are talking to the wrong people. I would try asking people that actually can do the CAD drawings in 3D and send that info to a CNC machine in whichever format that specific CNC needs. I just took a 24 hour course in Rhino CAD in SF. If you could find someone that has a decent command of a sophisticated program like Rhino, solid works, inventor, etc. then it should be pretty straightforward except the guess work of how long the machine will take to mill the pieces. Rhino jungle is a forum where you could post this question. I'm sure there are other forums for specific CAD programs too. Ever heard of 100k Garages? The site offers people to have things made by people that own CNC equipment. Here in San Francisco we also have Tech Shop which allows you to rent time on a CNC, laser cutter, plasma cutter, 3D printer/scanner, and many other sophisticated machinery. You could also outsource to them directly and they could ship to you.
From the original questioner:
Thanks - that is great information. I had no idea, as this CNC stuff seems like a mystery to me. I'll give it a try for the Boston area.
From contributor D:
Good point. Over the years, I have asked my machine dealer that sells and knows many CNC shops for contacts of shops that make it part of their business to do work for others. These are where I struck out. I have also asked lumber dealers, since they know who is doing what. The 100k Garages is interesting - thanks.
From contributor A:
I was able to make a good pyramid panel, and have an order to make 11 more.
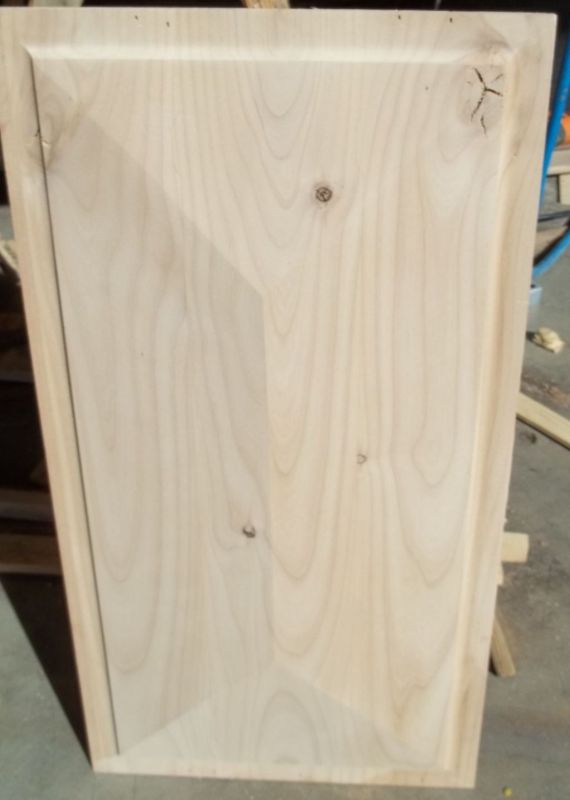
Click here for higher quality, full size image
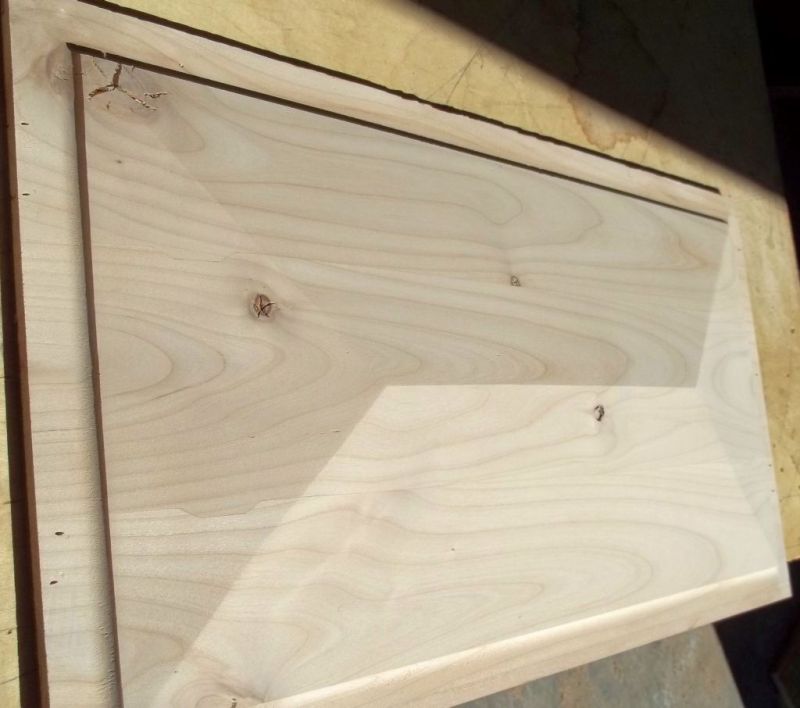
Click here for higher quality, full size image