Custom Cope and Stick Shaper Knives
A shaper owner considers cutter alternatives for making custom door parts. July 16, 2009
Question
I have a job coming in where I'll be building multiple doors and panels. In the past I made these up by using square parts and adding the glass stops to both sides of the panels. Since I'll be doing a fair amount this time I think it's time to get a shaper cutter made up for my profile.
So the question is: what should I be looking into for a one man shop that does more short runs than anything close to production? I've gradually progressed from the 3/4" bore cutters to the 1-1/4" Freeborn and occasional custom cutters. Now I'm wondering what the next logical step is. Should I have a solid cutter with carbide teeth made? Should I buy a cutterhead and have corrugated knives ground? Or should I look into insert tooling which from past threads sounds like it's probably too expensive for non-production shops? The profile is very simple. The picture below shows what the doors look like.
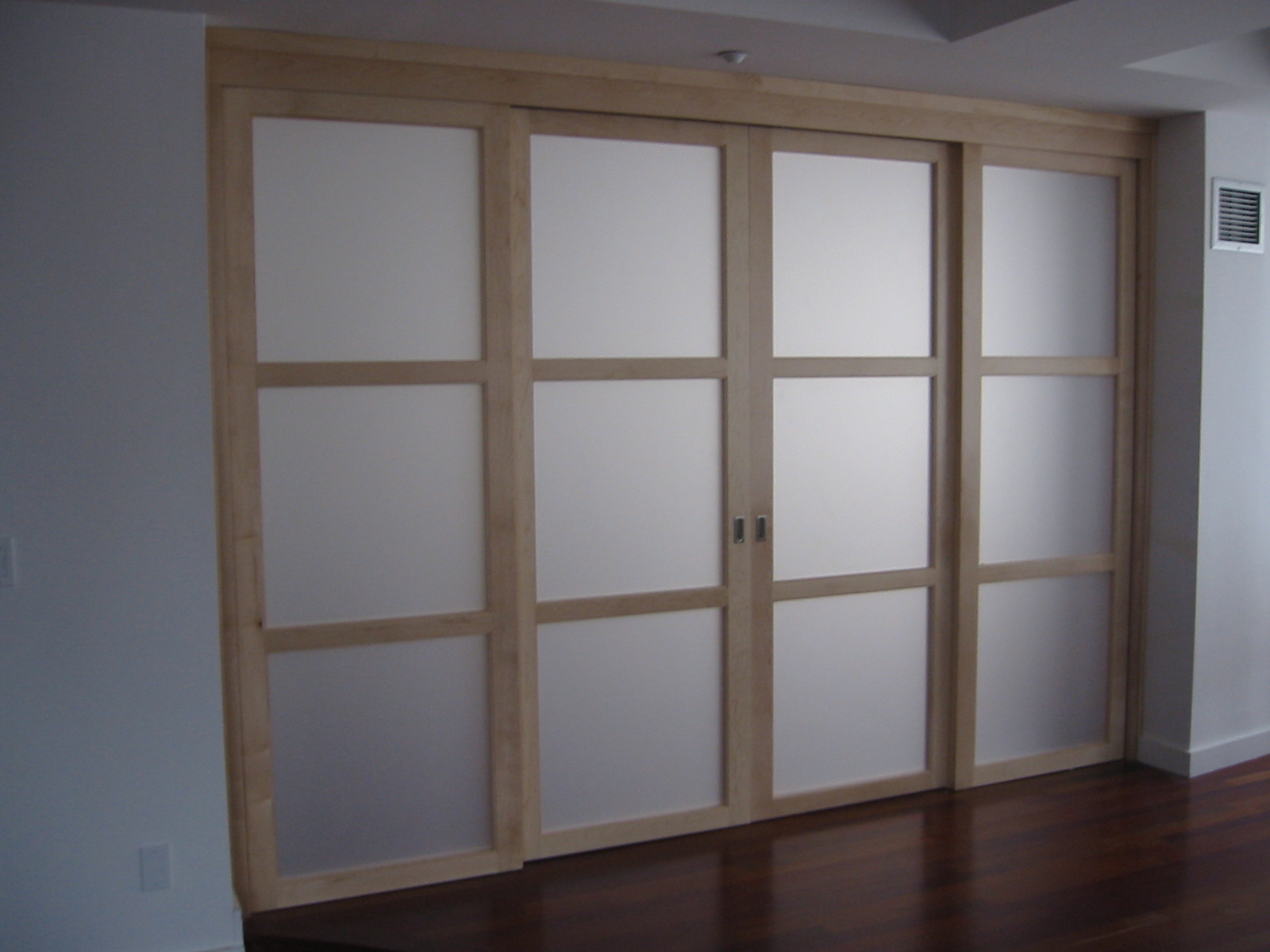
Click here for higher quality, full size image
Forum Responses
(Solid Wood Machining Forum)
From contributor M:
Freeborn (among many others) sells a good variety of brazed carbide door and sash cutters for both 1-3/8 and 1-3/4" doors. Great for small to medium size shop, nothing wrong with that type of setup. A corrugated head is versatile, but unless you have a profile grinder you are stuck having knives sharpened out. If you run HS steel that could be frequent although carbide is available, but that can get spendy. Also with that type of head your cutting circle can get quite large.
From contributor R:
As a short run shop, I'd be investing in a pretty standard corrugated head, and buying HSS knives ground to your profiles. HSS will last way longer than you'll need when properly set up and run. I've used this type set up to run several thousand feet of handrails in a stair shop I used to work at.
HSS simply cuts better than carbide. When properly set up and run I made handrails in one pass per side, even with huge profiles, and the cut quality was good enough to only require finish sanding after the milling. A power feeder is critical to the success of the set up. I typically milled the railing 1/32 oversize on each face and set the fence to remove the extra. This acts like a jointer and really improves the quality.
From the original questioner:
That's kind of what I was thinking. With the short runs I just don't see a return in spending a lot on individual cutters. I think I'll just look into picking up a corrugated head and having some knives ground.
From contributor D:
Think about tooling diameter and tenon lengths. It is best to tenon and cope in one go if your machine has the power. If not, you can rough the tenons on P-matic 2-a or t-saw or prior shaper operation, then do the cope and final size with dedicated heads. Two ways to go with cope and stick tools: multiple heads, each with its own thickness, function, pattern, etc. It’s expensive and hard to specify when you may not be sure of future work in this area. Or you could get a collection of cutters that can be stacked in different configurations for the job at hand. It’s less expensive, but versatile. Whatever you get, be sure it is carbide and the folks that make them will sharpen them and guarantee proper fitting.
From contributor K:
Don't underestimate the value of universal heads with disposable carbide tips. Like contributor R, I do a lot with corrugated back heads. When it comes to cope and stick profiles, disposable carbide tips are not terribly expensive and they give you a better cut as well as endless variety with in there range limit. If I'm not mistaken, although the heads cost a little more, the tips are less for a set than corrugated knives. I use a variety of head designs based on the type of profile needed, depth of cut, and etc. For a 6" crown I would use a 6" corrugated head. Disposable carbide for cope and stick, lock edge for a special deep bar rail I like to build etc. You will need a variety over time. I don't think the insert tooling is too expensive anymore because many shops are making the heads as well as the tips. I would not waste the money on custom brazed on carbide heads for short runs. I don’t think I would ever buy a brazed on tip head again anyway. Indexible heads allow a harder carbide to be used and that means they cut longer and again, the one head allows you multiple profile options for only the cost of grinding the profiles.
From the original questioner:
I hadn't even thought about doing the copes and tenons together with the shaper but that just might work. I'd have to have a larger diameter cutter made since I don't have a stub spindle, but I think if I go with separate stacked cutters it could work well. I did a quick sketch-up of the profile just to make sure I'm not overlooking something (else) obvious. I'm thinking for the cope a straight cutter followed by a 1/2" bushing, with the profile on top. The sticking cutter on the other hand is going to be sizeable. I'm guessing at least 1-1/8" tall with straight cutters underneath. Does this makes sense? If I don't do it this way I guess I'm going to have to use floating tenons which is a whole other train of thought I'll have to consider.
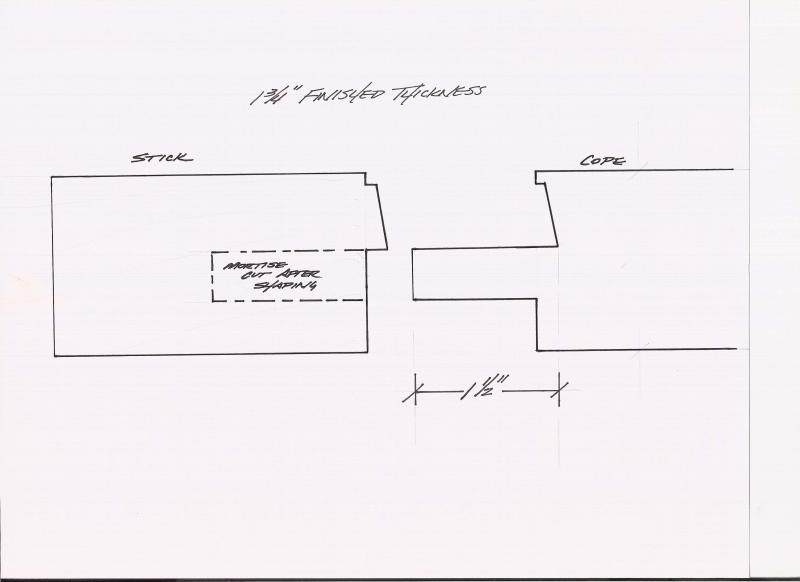
Click here for higher quality, full size image
From the original questioner:
My original thought was possibly corrugated steel knives as I wasn't taking into account correctly the M&T joint. If I did the floating tenons I could still use the corrugated knives as I think the profile may be a little large for a single brazed cutter? I may also look into the cost of the universal head with insert just to compare costs. Now that contributor D pointed out my mistake I'll have re-evaluate how I'm going to cut the M&T joints, and then price out the cutters to come up with the best solution.
From contributor D:
The cope and stick, with tenons getting in the way is a real problem. You are not the first to have missed some of the implications of doing this. Large diameter tooling is the quickest solution. Floating tenons is another solution, but running a slot mortiser, Maka or square chisel into end grain is a job I'd rather pass on.
Dowels are a solution if you can get the accuracy. You have to be dead on, or you are swinging a mallet, beating these things together.
Mortise and tenons do not need the end support, so the rails can slip a bit in the mortises, so the door can go together, rails to stiles, then pulled up in length where top rail is pulled to bottom rail, then the horizontal rails are clamped up tight. Mortises have some forgiveness. While I'm no advocate of sloppy work, we all need a little forgiveness every now and then.
From contributor K:
I have done the floating tenon on entry doors before with my little multi-router and as I said in your other post, it works but is hard on the machine (actually a P.C. router). Slot mortising end grain in general is a piece of cake with a heavy enough machine, like the Griggio. You could then limit the shaper tooling to just a sticking cut ground on corrugated steel and a 2" corrugated head and mortising tools. Once you have a slot mortiser, you find a lot of uses for it. That's why I love the multi-router.
From contributor J:
The solution is very simple. You need a shaper with a spindle length of at least 4". I suggest a sliding table shaper with a power feeder. Purchase a Pro-Scale. It is PLC driven to raise and lower the spindle. You can stack your cutters on the spindle. You can run all the rails and then hit the button and make your cope cuts. I suggest you buy multi-profile heads from Hickory Saw and Tool. They are equipped with carbide inserts with a profile of your choosing. Down the road when you have other jobs you can change your profiles and use the same head. Others suggest HSS knives and custom carbide cutter heads. I disagree - buy a multi-profile head with inserts and backer plates.
From contributor R:
Charles Schmidt sells large diameter discs for the shaper that would work quite well for coping/tennoning rails. They are used with corrugated knives and stacked using spacers and shims. A small bore standard corrugated cutterhead is used for the stiles. Various profiles in inlaid carbide or high speed steel ground to your pattern can be used. Very versatile and economical if you are starting small or doing limited production or "one-off" work. It all depends on the scale of your work. Whether you start simply as I have described or with dedicated insert tools as others have highlighted be sure to buy quality. Cheap tools usually are the most expensive route in the not so long run. A sliding table assembly such as the one Martin Woodworking Machinery sells is also a nice option for coping if your shaper does not have an integral slider.
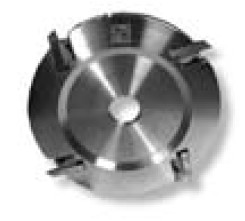
From the original questioner:
Thanks for all your advice guys, in the end I decided to go with a corrugated head, well, two actually. One for sticking and one for coping in an effort to save setup time. I had the knives made up by CG Schmidt and they're mounted and ready to go. My new (used) Bini slot mortiser is on the way and hopefully will be here soon. I decided to go this route as it seemed like I'd have more flexibility, which is important for my small shop setup. The corrugated heads should allow me to get a lot more use out of different profiles than the replaceable inserts. The slot mortiser I'm hoping will open up new possibilities with other types of work as well.