Custom Architectural Woodwork on the CNC
A request for ideas for making some custom quarter-round mouldings turns into an extended discussion of custom techniques and the value of hand labor versus computerized production. February 19, 2008
Question
I need four pieces of tulipwood, 2.4M long, 65mm x 65mm, machined into 1/4 round profile. Just like very large quadrant moulding. My deadline is too tight to wait to get cutters for a spindle moulder made up. I could angle the blade on my table saw and rip a series of bevels on the square stock and finish by hand, but I really don't want to! Is there any other way of doing this, maybe some router jig or template? Is this feasible on a CNC?
Forum Responses
(Architectural Woodworking Forum)
From contributor D:
If I had the pleasant job of working with such wonderful wood as a dalbergia, I'd get out the hand planes and enjoy every minute. After S4S, I'd use the table saw to rough in the shape in 3 to 5 passes, then lock up the bench vise and plane away. I'd save the shavings for the showroom, since most people have never smelled a true rosewood. I'd even leave some of the hand scraper marks to indicate the level of skill that made the parts.
Just my opinion, but a fabulous wood like tulipwood should be worked by hand where possible, just as it has been for centuries. Sure, a CNC could be programmed to do it, but then the maker is taken out of the equation. And, the sawing and hand planing will be done well before the programmer has things figured out.
From contributor L:
"And, the sawing and hand planing will be done well before the programmer has things figured out."
Unlikely. What kind of programmers do you know? I appreciate quality hand work as much as the next guy, but the questioner said he had a quick deadline. If you were able to charge whatever you wanted per piece and had all the time in the world... no problem. However, it doesn't sound like the questioner can make love to this piece.
From contributor D:
I have asked CNC people for pricing for carvings, compound curves of S4S, curves of profiled things and so forth. They all wanted thousands of dollars before the machine was even turned on or tooling made. The carving quote request came back at over $11,000 for a 12" sample!
These sticks are about 6-1/2' long, with two faces 90 degrees to each other, each about 2-1/2". If I couldn't do these (as described earlier) in less than four hours, then I'd better retire.
Being a trained woodworker, another person would say, "Four of 'em? Heck, just glue them together with kraft paper between them, and turn 'em on the lathe!" Then split them apart. If he was under 35, he'd add, "duh!"
I view woodworking as problem solving, and the solution rarely involves asking someone else to do it. I have found that absolutely no one cares about my work more than me, so I need to be resourceful and flexible, and still get the job done. So, I'll bite. Anyone out there want to quote the work as stated here on the forum? Don't forget to stipulate the finished surface and what it would look/feel like. You also don't have to make love to it, unless you want to.
From contributor L:
Well, with your experience with CNC guys, I now understand you statement. $11k is insane for the part you described. I have done extremely complicated parts myself, and also had them outsourced to shops in the US for much lower costs. I appreciate the fact that you want to keep a direct connection with your product. The questioner just does not seem to have the ability right now. I've included an image of some exterior brackets I engineered, and had a gentleman in the great lake area cut on his CNC because we were too busy. It was something like around 2k each and that included material. Reasonable CNC programming is out there.
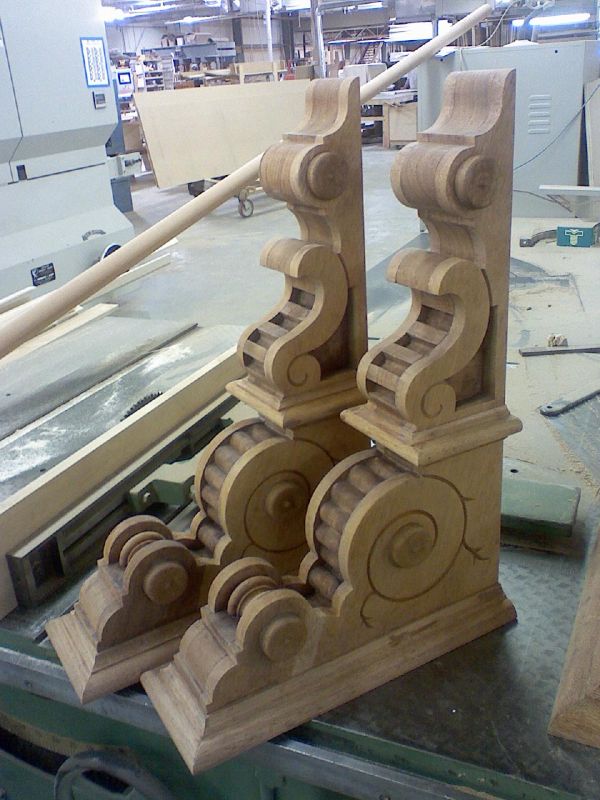
Click here for higher quality, full size image
From contributor R:
I have done a lot of curved and circular carving on CNC machines, and this project looks fairly straightforward. I would probably be able to make money cutting these at $250-300 per stick; this would include the glue-up, programming, cutting and finish sanding. This would not include the cost of the wood, or shipping. The finish would be comparable to a turned and sanded finish.
The problem with these kinds of jobs is that my schedule is just as busy as yours, so if you want a fast turn-around, you usually have to pay a premium, just like if someone wanted you to bump your schedule for them.
Contributor D, I don't feel like I am out of the equation when I program and cut wood on the CNC. I get to do some pretty interesting projects that take some figuring and problem solving, and I usually do the cutting and finishing. The CNC is just another tool, and must be guided by a person, and most carved parts still need to be detailed, sanded or assembled by someone with a feel for what they are doing. The router roughs out the parts in the way that apprentices used to do in the old days.
From contributor D:
I don't intend to dismiss all CNC machines and operators as useless bits of techno. They obviously have their rightful place in the world of wood machining, and excel at many tasks. And a quick, flexible, thinking operator with a good machine would be worth their weight in gold as we see basic skills decline in most shops.
My remarks stem from a certain frustration I feel when I see otherwise earnest woodworkers resort to "outsource to CNC" as the solution to any problem that comes their way. Adopting a "let someone else do it" attitude robs the shop of the important ability to solve problems and invest in their own know-how. The knowledge, money, and reputation all stay within the shop. This may only matter if the shop is skills based and is concerned with employee and skill development. Should skill be outsourced?
We are doing curved French molded raised panel and frame assemblies this week, and are one of few shops that will even attempt it. We find it sort of easy to do since we developed the know-how years ago. Today it is common for us, but still foreign/impossible to other shops. I think of this know-how as a sort of equity of knowledge - a resource to utilize and build upon. By the way, the curved panels are just part of a much larger project that came to us because of our know-how.
At about 275.00 a quadrant, $1100.00 for the job, our shop rate puts this labor at just under 16 hours. As stated earlier, if I couldn't do it in 4 hours (okay, I should have said 6 hours), it's time to move on. Turning them on the lathe would be a better product, and even less time. Then I'd still have those marvelous shavings to let people know why rosewood is called rosewood.
From contributor P:
Okay, am I missing something here? This is basically four straight pieces of tulipwood, 2.5 in square x 95 inches with a full quarter round profile (2.5 in rad approximately). Straight pieces, right? Obviously the custom knife is the way to go. The bevel approach will work and you can quickly grind a scraper to help. What about hose clamping the four pieces together and creating a lathe using a router and a wide straight cut bit? Basically rotate the four pieces under a router to create a large cylinder. You would have to make the jig - that would take a few hours. CNC could do it as well, quickly, if you have someone in the area.
From the original questioner:
Thanks for all the responses. I'm afraid my UK terminology has been somewhat misleading - I apologize. Over here, everyone refers to Liriodendron tulipifera as tulipwood. So nothing exotic enough to warrant wanting to make love to it! Just soft and cheap - whatever you call it in the US - poplar or whitewood. In the end I've had to wait and someone is going to grind up the cutters and run it on a spindle moulder. Thanks for all the advice; nothing like it in the UK!
From contributor S:
"I'd even leave some of the hand scraper marks to indicate the level of skill that made the parts."
I love it! I had a lady tell me recently that she loved the way her kitchen (my cabinetry) looked "handmade," instead of the flawless factory perfection she'd seen at Home Depot.
Having said that, I'd give my left you-know-what for a good CNC. Just like the nail gun supplemented the hammer, a CNC is a marvelous tool with a specific purpose.
From contributor D:
As a logical extension of the discussion, is anyone using a CNC to replicate hand planing, scraping or similar evidence of hand work? When I left a big shop to go to my one man shop, with its more primitive methods, I worked hard to make my products look as cleanly machined as the big shop stuff. Then I realized a large part of my market valued hand work and wanted to see evidence of the hand of the maker. Now we know when and where to leave such evidence, and do so genuinely. It is perceived as a better product and saves us some time.
From contributor L:
I have a moulder aggregate for our CNC, and by editing a spline, I imagine I could use a moulder knife to replicate to some degree the marks you would achieve by hand planing or scraping. We don't do this but I'm sure with a little work we could do it. That's actually a really good question. It looks like I have a project to consider.
From contributor S:
Customer perception is everything. No question my cabinets are better built than the twenty-year-old stuff I'm ripping out - but they still lasted twenty years, didn't they? And the lady didn't call me because her dishes were falling out on the floor. This discussion takes us back to the difference between "wants" and "needs."
I'm just a one truck parade, but if a CNC will trim one employee off the payroll, it will easily pay for itself. I could still do the visible elements by hand. I appreciate the accuracy and consistency that a CNC will deliver - heck, we could build cabinets without a tape measure if we had to... by why should we?
From contributor F:
Credit is still due to a craftsman who uses a CNC. You probably would have to do the whole process yourself to understand what we mean. You still have to think and plan and solve problems. Really no different than the process of using non-CNC woodworking equipment. I mean, does anyone think less of someone who powerfeeds a shaper instead of hand feeding? CNC is like that - you still have to handle the wood materials before and after the machining, install the proper cutters, etc.
I do agree that there is an excess of "sub it out to another shop" as stock advice for anything trickier than a table saw cut these days. I too see a lot of value in doing as much work as possible in house. As said, the money, skill and knowledge all stay home. I realize there are always two schools of thought, though. One school sees the value and the benefit of expanding skill and knowledge along with the love of a good challenge. The other sees woodworking as more black and white... nothing but the bottom line.
From contributor J:
I don't think it's "nothing but the bottom line" - it just doesn't make sense not to use a CNC if you can. It will make a better product in the right hands. I don’t think planing a gable of solid lumber by hand makes the gable any better than if it was thickness planed – certainly it has more labor in it and therefore it costs more to make, but as both have to be sanded or scraped after planing to remove tool marks, the one out of the planer has got to be the more precision piece of lumber, that in the end will yield a better cabinet component. A customer would have to be very knowledgeable to understand and appreciate (enough to pay extra) the work and inherent value of hand planed pieces of wood, and I don't think there are enough of those type of customers out there to support a business based on that type of work. There is an argument to be made about certain carved or ornamental work on fine furniture; it certainly has much less value (in my opinion almost no value) if it was CNC cut. Anyway, in this case it would be much faster and easier to make them by hand, because you’d have to outsource the CNC work.
From contributor F:
Right - I don't think many (if any) around here would think that a hand planed panel was any better than a machined planed panel. But I don't agree that it is senseless for someone like me to refrain from outsourcing my work in every case where somebody else has a better or faster tool than I do. That's life... somebody else will always have bigger and better toys than we have. To me, working with what I do have is part of the business and part of living. To some makers this may be seen as old school logic.
The other thing is, there are cases where I would job shop part of a project out to another company. It just depends on factors like quantity... how often this sort of work comes up, etc.
You shouldn't be too extreme either way. I see some posters on this forum get the advice to outsource jobs that could be done in house with a little ingenuity in far less time than it would take to make the phone calls and load and unload material twice plus travel time.
To be clear, in this day and age, if the only tool a shop owner has to thickness panels with is a hand plane, I don't think he should outsource his thicknessing work. I think he should buy an entry level thickness planer.
From contributor J:
You're absolutely right, he should get a planer right away, no question. As for outsourcing, if I can truly get it done for less by outsourcing, why wouldn't I do it?
From contributor F:
If it's only about the money for you, you should outsource it. However, some woodworkers like a challenge, like to attempt things they haven't tried before. Each time they leave their comfort zone and delve into new woodworking territory, they learn something new. It's a different sort of satisfaction than coming in at the exact target profit margin. Some guys take pleasure from devising shop methods and fixtures that pretty much force a piece of material to become exactly what they will it to become.
Naturally, I don't advocate getting in so far over your head that you lose the farm. I have lost a few bucks from time to time, but I use common sense to keep me from biting off way more than I could ever hope to chew.
Lastly, for some of us, it's about quality and control. Very few outsource suppliers care as much about quality as the buyer does. I would rather slim down my profit margin than sell something that really isn't up to my standards.