Condensate Drain Problems
Ideas for keeping your air tank dry during operation. December 7, 2008
Question
We have a rotary screw compressor and a 200-gallon tank. We get an extreme amount of water in the tank this time of year. We have an automatic drain at the bottom of the tank, but the tank is old and has rust in it and the rust clogs up the filter all the time. Then the tank fills up with water. I pulled the automatic drain off and just put a hose on it and have been keeping it open a little. I did not think that this was a long-term solution so I purchased a large water filter and connected it to the drain outlet. I attached the automatic drain to the large water filter. It did not take long for the water filter to fill up with water. Every minute or so, the auto drain opens and pulls off some of the water in the filter.
I am just wondering if this is really going to work, or if I will have a problem later on. Am I forgetting something important? If the water keeps draining from the bottom of the air tank, it should work just fine. Is there a better solution?
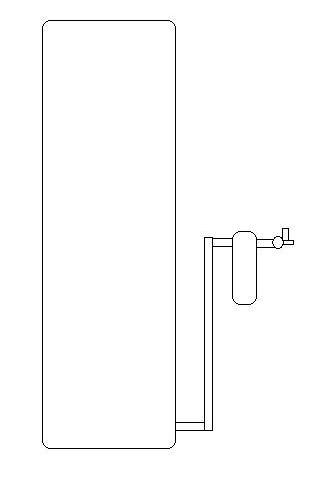
Click here for full size image
Forum Responses
(Cabinetmaking Forum)
From contributor R:
I don't think it is a problem putting a filter before your auto drain valve but the valve has to be below the bottom of the tank in order for the float chamber to fill and open the drain valve.
From contributor M:
The type of auto drain that I have is just a solenoid that opens a valve at set intervals for a set amount of time. It does not use a float.
From contributor R:
That type of drain valve could go anywhere. So it just drains whether it needs to or not? Seems wasteful.
From contributor D:
Is there not a drain cock on the underside of your tank (bottom, dead center)? The location you show only keeps water from filling the tank when the idea of the autodrain is to keep it dry. If there is a drain there (or a plug), raise the tank to make it accessible. Drain tank and flush well to clear the crud out. Install the autodrain on the underside drain.
I think ours runs about five to ten seconds on about a ten minute cycle. That junk you're filtering is also going the other way and will eventually cause problems in tools and (worse) paint lines. It doesn't matter how many filters you put in.
From contributor J:
We use a refrigerated compressed air dryer in between our compressor and the air lines. Are you using something similar? You need something to remove all the moisture from the air lines before it goes into any tools or equipment.
From contributor L:
Our system goes from the rotary screw compressor through an air to air cooler, coalescing filter, refrigerated drier, then the regulator before going into a loop system of copper piping. Every morning before the compressor is started we manually open the drain on the tank and the coalescing filter. The refrigerated drier has a timed auto drain. It is set for a short blow down time since most of the water has condensed out before it gets there. Timed drains are wasteful but are more reliable. All the condensate goes into a filter that separates the oil so the water can be let into the sewer. Ideally our air to air drier would be after the coalescing filter but it is located on top of the compressor room and used to pull cooling air through the room. We also have desiccant driers in front of several expensive major tools just to make sure! They color change when they need service.